A key-shaped groove flow regulating damping cylinder for intelligent knee joint
A flow adjustment and knee joint technology, applied in the field of damping cylinder structure, can solve the problems of inability to reach the designated position, large axial load of the motor, increased power consumption, etc., to avoid failure of damping adjustment, continuous damping adjustment, and avoid motor failure. step effect
- Summary
- Abstract
- Description
- Claims
- Application Information
AI Technical Summary
Problems solved by technology
Method used
Image
Examples
Embodiment Construction
[0026] In order to make the technical means and effects realized by the present invention easy to understand, the present invention will be described in detail below in conjunction with the embodiments and accompanying drawings.
[0027] figure 1 It is a cross-sectional view of a key-shaped groove flow regulating damping cylinder for an intelligent knee joint in an embodiment of the present invention.
[0028] Such as figure 1 As shown, a key-groove flow regulating damping cylinder 100 for a smart knee joint in this embodiment has a cylinder portion 10 , a piston assembly 20 , a spring assembly 30 and a flow regulating assembly 40 .
[0029] The cylinder part 10 has a cylinder body 11 provided with two parallel hydraulic oil passages, a steel sleeve 12 fixed inside the cylinder body by a sealing ring, and a cylinder head 13 fixed on the upper end of the cylinder body 11 by threads.
[0030] The piston assembly 20 is disposed in the cylinder body 11 and has a piston rod 21 an...
PUM
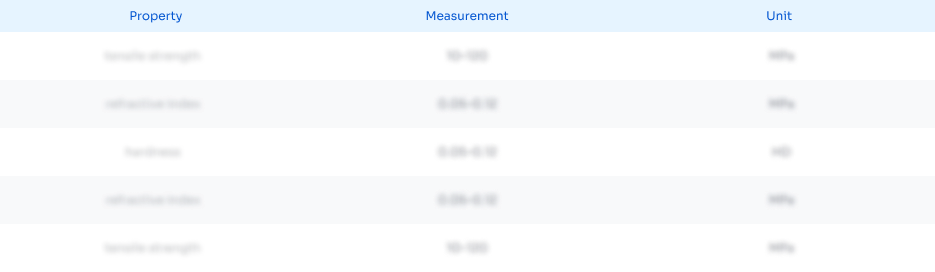
Abstract
Description
Claims
Application Information

- R&D
- Intellectual Property
- Life Sciences
- Materials
- Tech Scout
- Unparalleled Data Quality
- Higher Quality Content
- 60% Fewer Hallucinations
Browse by: Latest US Patents, China's latest patents, Technical Efficacy Thesaurus, Application Domain, Technology Topic, Popular Technical Reports.
© 2025 PatSnap. All rights reserved.Legal|Privacy policy|Modern Slavery Act Transparency Statement|Sitemap|About US| Contact US: help@patsnap.com