Detecting method and monitoring system for coupling fault of rotating machine
A technology for coupling faults and rotating machinery, applied in general control systems, control/regulation systems, instruments, etc., can solve problems such as poor fault detection accuracy, and achieve the effect of being convenient for practical application
- Summary
- Abstract
- Description
- Claims
- Application Information
AI Technical Summary
Problems solved by technology
Method used
Image
Examples
Embodiment 1
[0121] Embodiment 1: A comprehensive test bench for fault diagnosis of wind turbine power transmission is adopted, and vibration signals of coupling faults of bearings and gears of parallel-axis gearboxes are collected through acceleration sensors on the test bench. Vibration signal, make training data set and test data set.
[0122] There are 12 different fault types in the collected vibration signals, see Table 2. It can be seen from Table 2 that the 12 types of faults are: (1) normal condition N, (2) inner ring bearing fault IF, (3) roller bearing fault condition RF, (4) outer ring bearing fault OF, (5) Coupling failure IRO for inner ring, ball and outer ring condition, (6) coupling failure for ball bearing and notched gear condition (RCH), (7) coupling failure for ball bearing and cracked gear condition (RCR), (8) outer ring Coupling failure occurs in bearing and tooth-missing gear state (OCH), coupling fault occurs in (9) outer ring bearing and cracked gear state (OCR), ...
Embodiment 2
[0131] Embodiment 2: In order to verify that the rotating machinery coupling fault monitoring system of the present invention can meet the real-time requirements of online monitoring, the relationship between the time and the batch size when testing the diagnostic data of the monitoring system is tested. By testing on different batch sizes, it can be obtained that the time required for the proposed system to diagnose a signal is about 44ms, and the sampling frequency of the acceleration sensor that collects mechanical vibration signals in the wind turbine power transmission fault diagnosis comprehensive test bench is 5.12KMz , each sample signal takes 2048 sampling points, and the relationship between time and batch size is shown in Table 5. It can be seen from Table 5 that the rotating machinery coupling fault monitoring system of the present invention can well meet the real-time requirements.
[0132] table 5
[0133] batch size
PUM
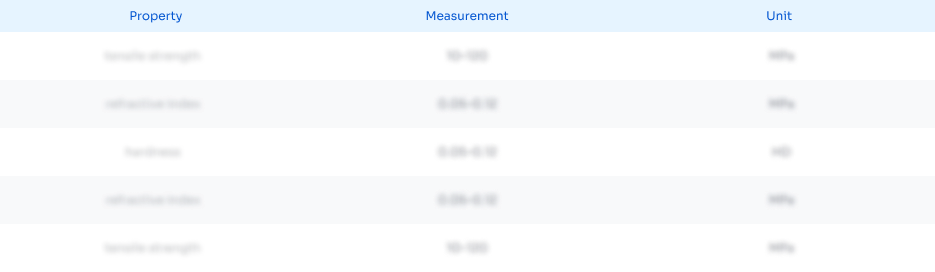
Abstract
Description
Claims
Application Information

- R&D
- Intellectual Property
- Life Sciences
- Materials
- Tech Scout
- Unparalleled Data Quality
- Higher Quality Content
- 60% Fewer Hallucinations
Browse by: Latest US Patents, China's latest patents, Technical Efficacy Thesaurus, Application Domain, Technology Topic, Popular Technical Reports.
© 2025 PatSnap. All rights reserved.Legal|Privacy policy|Modern Slavery Act Transparency Statement|Sitemap|About US| Contact US: help@patsnap.com