Planning method of industrial robot joint space synchronous movement
An industrial robot and joint space technology, applied in manipulators, manufacturing tools, program-controlled manipulators, etc., can solve the problems of non-smooth transition of motion speed and acceleration, poor anti-shake performance, etc., and achieve good anti-shake performance, easy to implement, and method simple effect
- Summary
- Abstract
- Description
- Claims
- Application Information
AI Technical Summary
Problems solved by technology
Method used
Image
Examples
Embodiment Construction
[0055] Below in conjunction with accompanying drawing, method of the present invention is described in further detail:
[0056] Running this method in the robot motion controller is to know the starting point and end point of each joint motion of the robot expected by the user, and plan the motion state of each joint of the robot at each moment between these two points to ensure that the joints of the robot move synchronously. And its speed, acceleration smooth transition.
[0057] Such as figure 1 As shown, this method is a program instruction running in the motion controller, and its running process is:
[0058] Step [1] Start the motion controller;
[0059] Step [2] Obtain the end point sEndP.A of the desired joint movement of the robot i and the starting point sStaP.A i ;
[0060] Step [3] Calculate the maximum time required for planning MaxT based on the known starting point and end point; the specific steps are:
[0061] Step [3.1] Calculate the angle θ that each m...
PUM
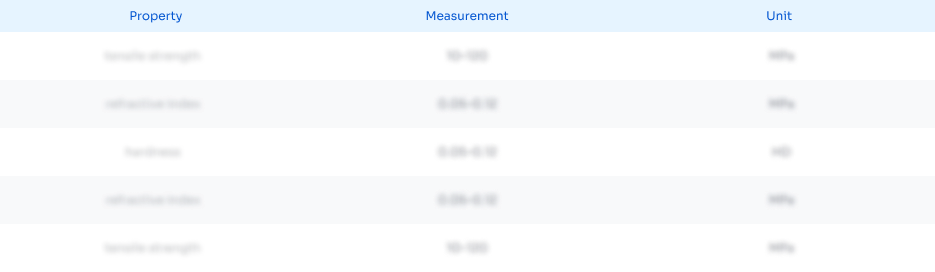
Abstract
Description
Claims
Application Information

- R&D
- Intellectual Property
- Life Sciences
- Materials
- Tech Scout
- Unparalleled Data Quality
- Higher Quality Content
- 60% Fewer Hallucinations
Browse by: Latest US Patents, China's latest patents, Technical Efficacy Thesaurus, Application Domain, Technology Topic, Popular Technical Reports.
© 2025 PatSnap. All rights reserved.Legal|Privacy policy|Modern Slavery Act Transparency Statement|Sitemap|About US| Contact US: help@patsnap.com