Electromechanically controlled 3D camera with crossed light paths
A camera and optical path technology, applied in the field of electromechanically controlled cross optical path 3D cameras, can solve the problem that the microscope does not have zoom and focus functions, and achieve the effect of comfortable observation and real and clear 3D images
- Summary
- Abstract
- Description
- Claims
- Application Information
AI Technical Summary
Problems solved by technology
Method used
Image
Examples
Embodiment 1
[0023] An electronically controlled cross-optical 3D camera, such as figure 1 As shown, it includes two lens barrels 18 installed in parallel. The top of each lens barrel 18 is equipped with an optoelectronic sensor 3. The top of the optoelectronic sensor 3 is provided with an optoelectronic sensor output port 1 and an optoelectronic sensor power input port 2. The rotation adjustment ring on the outer wall of the barrel 18 is connected by a variable optic chiasm linkage rod 4. One end of the variable optic chiasm linkage rod 4 is provided with an optic chiasm linkage power device 5, and the middle of the outer walls of the two lens barrels 18 are respectively provided with The steering gears 7 are equipped with a zoom gear 10 at the bottom of each steering gear 7, and guide laser lights 11 are also provided on the outer walls of the two lens barrels 18. The two steering gears 7 are connected by a zoom universal coupling 9, and the zoom universal A zoom power device 8 is connecte...
Embodiment 2
[0027] As the second embodiment of the present invention, such as figure 2 with image 3 As shown, the optic cross connecting rod power unit 5, the zoom power unit 8 and the focus power unit 14 all include a cylinder 141, and the cylinder 141 is provided with a piston rod 142.
[0028] Further, the focus linkage rod 15 is provided with two rotating holes 151, and the distance between the two rotation holes 151 is adapted to the distance between the two objective lenses 13. The focus linkage rod 15 is close to the focus power device 14 One end is provided with a fixed sleeve 152, the fixed sleeve 152 and the focusing linkage rod 15 are integrally formed, the fixed sleeve 152 is provided with a fixed hole 153, the outer wall of the objective lens 13 is provided with a screw hole 131, and the piston rod 142 is far away A fixing hole 153 is also opened on the circumferential surface of one end of the cylinder 141, and the piston rod 142 and the fixing sleeve 152 are inserted and fit...
PUM
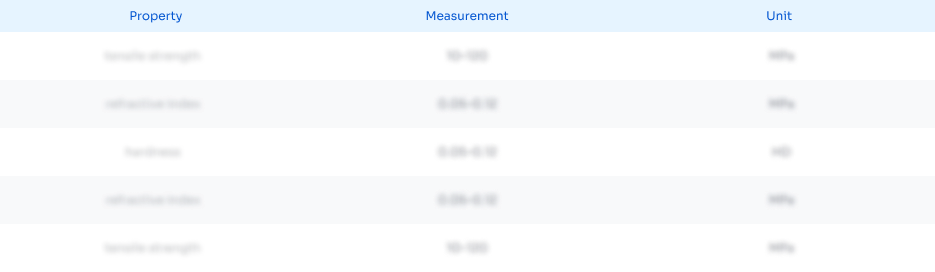
Abstract
Description
Claims
Application Information

- R&D
- Intellectual Property
- Life Sciences
- Materials
- Tech Scout
- Unparalleled Data Quality
- Higher Quality Content
- 60% Fewer Hallucinations
Browse by: Latest US Patents, China's latest patents, Technical Efficacy Thesaurus, Application Domain, Technology Topic, Popular Technical Reports.
© 2025 PatSnap. All rights reserved.Legal|Privacy policy|Modern Slavery Act Transparency Statement|Sitemap|About US| Contact US: help@patsnap.com