Direct force detecting device, control system and direct force control exoskeleton robot
An exoskeleton robot and control system technology, applied in the field of human dynamics, can solve the problems of high precision of rotary joints, high manufacturing process requirements, complicated design of exoskeleton control strategies, and inability to complete power-assisted actions, etc., and achieves simple and convenient system design. Light weight, improved safety and comfort
- Summary
- Abstract
- Description
- Claims
- Application Information
AI Technical Summary
Problems solved by technology
Method used
Image
Examples
Embodiment Construction
[0037] In order to have a clearer understanding of the technical features, purposes and effects of the present invention, the specific implementation of the present invention will now be described with reference to the accompanying drawings
[0038] The direct force detection device includes a contact force sensor (90), a human leg baffle (110), a binding device (120) and an exoskeleton leg link (140); the binding device (120) is installed on the human leg On the baffle (110); one end of the contact force sensor (90) is fixedly connected to the human leg baffle (110), and the other end is connected to the exoskeleton leg link (140).
[0039] A sponge pad (130) is provided inside the binding device (120) to prevent discomfort or injury when the exoskeleton is released from the human body.
[0040] The connection mode between the contact force sensor (90) and the exoskeleton leg link (140) is hinge connection.
[0041] The direct force control system includes a force sensor, a ...
PUM
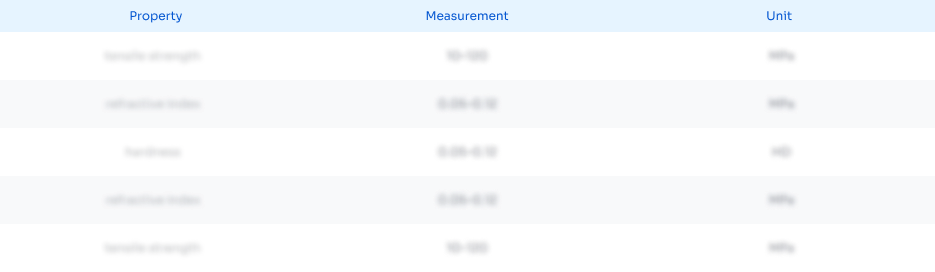
Abstract
Description
Claims
Application Information

- R&D
- Intellectual Property
- Life Sciences
- Materials
- Tech Scout
- Unparalleled Data Quality
- Higher Quality Content
- 60% Fewer Hallucinations
Browse by: Latest US Patents, China's latest patents, Technical Efficacy Thesaurus, Application Domain, Technology Topic, Popular Technical Reports.
© 2025 PatSnap. All rights reserved.Legal|Privacy policy|Modern Slavery Act Transparency Statement|Sitemap|About US| Contact US: help@patsnap.com