Preparation method of 3D printing photocatalysis device
A 3D printing and photocatalysis technology, applied in the field of environmental treatment, can solve the problems of easy shedding of catalysts, difficult recycling, and high loading rate, and achieve the effect of preventing powder photocatalytic diffusion, simple and efficient preparation method, and difficult to recover.
- Summary
- Abstract
- Description
- Claims
- Application Information
AI Technical Summary
Problems solved by technology
Method used
Image
Examples
Embodiment 1
[0021] (1) After mixing 6kg PLA and 4kg PVA, they are melted and extruded to granulate by screw. The parameters of the twin-screw extruder are: 100°C in zone 1, 110°C in zone 2, 130°C in zone 3, 140°C in zone 4, and 140°C in zone 5 150°C, 160°C in the sixth zone, 170°C in the seventh zone, 170°C in the eighth zone, 160°C in the ninth zone, 150°C at the die head, and a rotation speed of 200 rpm. Traction into 3D printing wire, the parameters of the wire machine are: 160°C in the first zone, 170°C in the second zone, 170°C in the third zone, 160°C in the fourth zone, and the speed is 50rpm. The diameter is 1.75mm, and the hole-forming wire is obtained;
[0022] (2) Pull 10kg PETG into a 3D printing wire through a wire machine. The parameters of the wire machine are: 200°C in the first zone, 210°C in the second zone, 200°C in the third zone, 200°C in the fourth zone, and the rotation speed is 50 rpm. The extruded silk is water-cooled Cooling, pulling and controlling the wire dia...
Embodiment 2
[0026] (1) Mix 7kg PLA and 3kg NaCl and then melt and extrude to granulate through the screw. The parameters of the twin-screw extruder are: 100°C in the first zone, 110°C in the second zone, 130°C in the third zone, 140°C in the fourth zone, and 140°C in the fifth zone 150°C, 160°C in the sixth zone, 170°C in the seventh zone, 170°C in the eighth zone, 160°C in the ninth zone, 150°C at the die head, and a rotation speed of 200 rpm. Traction into 3D printing wire, the parameters of the wire machine are: zone 1 160°C, zone 2 170°C, zone 3 170°C, zone 4 160°C, rotation speed 50 rpm, the extruded filament is cooled by water, and is drawn and controlled by the tractor. The diameter of the wire is 1.75mm, and the hole-forming wire is obtained;
[0027] (2) Pull 10kg PETG into a 3D printing wire through a wire machine. The parameters of the wire machine are: 200°C in the first zone, 210°C in the second zone, 200°C in the third zone, 200°C in the fourth zone, and the rotation speed i...
Embodiment 3
[0030] (1) Mix 7kg PBAT, 3kg Na 2 CO 3 After mixing, it is granulated by screw melt extrusion. The parameters of the twin-screw extruder are: 80°C in the first zone, 90°C in the second zone, 100°C in the third zone, 110°C in the fourth zone, 120°C in the fifth zone, 130°C in the sixth zone, and 130°C in the seventh zone. Zone 135°C, zone 8 130°C, zone 9 120°C, die head 110°C, rotation speed 200 rpm, extrude and granulate to obtain wire masterbatch, and pull the obtained pellets into 3D printing wire through a wire machine, wire machine parameters It is: 120°C in the first zone, 130°C in the second zone, 130°C in the third zone, 120°C in the fourth zone, the rotation speed is 50 rpm, the extruded silk is cooled by water, pulled by the tractor and controlled to control the wire diameter of 1.75mm, and the pore-forming wire;
[0031] (2) Pull 10kg of TPU into a 3D printing wire through the wire machine. The parameters of the wire machine are: 160°C in the first zone, 170°C in t...
PUM
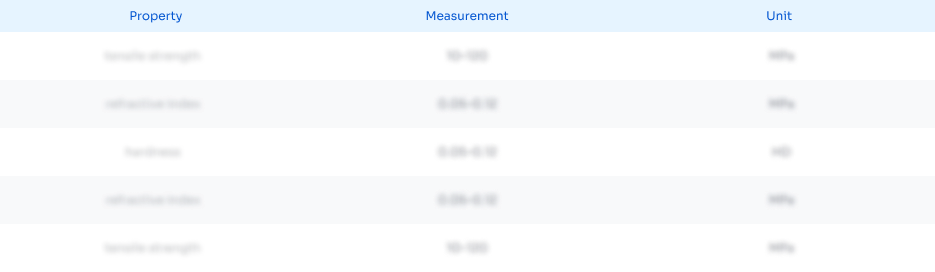
Abstract
Description
Claims
Application Information

- R&D
- Intellectual Property
- Life Sciences
- Materials
- Tech Scout
- Unparalleled Data Quality
- Higher Quality Content
- 60% Fewer Hallucinations
Browse by: Latest US Patents, China's latest patents, Technical Efficacy Thesaurus, Application Domain, Technology Topic, Popular Technical Reports.
© 2025 PatSnap. All rights reserved.Legal|Privacy policy|Modern Slavery Act Transparency Statement|Sitemap|About US| Contact US: help@patsnap.com