Kinematic method for improving absolute positioning precision of industrial robot
An absolute positioning accuracy, industrial robot technology, applied in manipulators, manufacturing tools, program-controlled manipulators, etc., can solve the problems of limited compensation accuracy, limited application range, geometric parameter errors, etc., and achieve the effect of achieving the accuracy requirements of the error threshold
- Summary
- Abstract
- Description
- Claims
- Application Information
AI Technical Summary
Problems solved by technology
Method used
Image
Examples
Embodiment Construction
[0037] In order to make the technical means, creative features, goals and effects achieved by the present invention easy to understand, the present invention will be further elaborated below.
[0038] like Figure 1 to Figure 4 As shown, a kinematics method for improving the absolute positioning accuracy of industrial robots includes the following steps:
[0039] S1: First establish the error model of the robot’s geometric parameter ɡ, collect the pose error ΔX of the robot’s end in the robot’s workspace, and use the identification method to identify the robot’s DH geometric parameter error Δɡ; the robot’s end position X and The kinematic relationship between joint variables q is:
[0040] X=f(q,ɡ) (1)
[0041] After considering the geometric parameter error Δɡ, the kinematic relationship between the end position of the robot and the joint variables is:
[0042] X+ΔX=f(q,ɡ+Δɡ) (2)
[0043] Through the relationship (1) and (2), the relationship between the pose error ΔX at ...
PUM
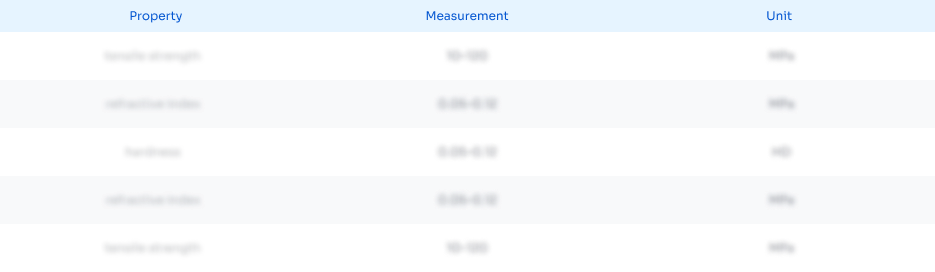
Abstract
Description
Claims
Application Information

- R&D Engineer
- R&D Manager
- IP Professional
- Industry Leading Data Capabilities
- Powerful AI technology
- Patent DNA Extraction
Browse by: Latest US Patents, China's latest patents, Technical Efficacy Thesaurus, Application Domain, Technology Topic, Popular Technical Reports.
© 2024 PatSnap. All rights reserved.Legal|Privacy policy|Modern Slavery Act Transparency Statement|Sitemap|About US| Contact US: help@patsnap.com