Granulator
A technology of granulator and bearing seat, which is applied in the direction of granulation in the rotary tank, etc., can solve the problems of rising production cost and declining output rate of products produced by smelting enterprises, so as to increase output rate, avoid waste of production raw materials, and be convenient to use Effect
- Summary
- Abstract
- Description
- Claims
- Application Information
AI Technical Summary
Problems solved by technology
Method used
Image
Examples
Embodiment Construction
[0018] exist figure 1 , figure 2 , image 3 In the illustrated embodiment, the support 12 is supported by inclined legs 9, the middle part of the support 12 is the bearing frame 10, the rear straight beam 4, the left straight beam 13 are welded on the support 12, the back straight beam 4, the left straight beam 13 The upper end is welded with the L-shaped beam 1; the upper end of the connecting plate 3 is connected with the L-shaped beam 1 through a screw rod, and the lower end of the connecting plate 3 is connected with the baffle plate 2 through a screw rod. There is a bearing seat 8 on the bearing seat frame 10, and a bearing 7 is arranged in the bearing seat 8. The lower part of the shaft 6 passes through the bearing 7, the bearing seat 8, and the bearing seat frame 10. The shaft 6 is supported by the bearing 7, and the upper end of the shaft 6 is connected with the screw rod. Rotary cylinder 5 is connected, and the lower end of axle 6 is equipped with belt pulley 11. ...
PUM
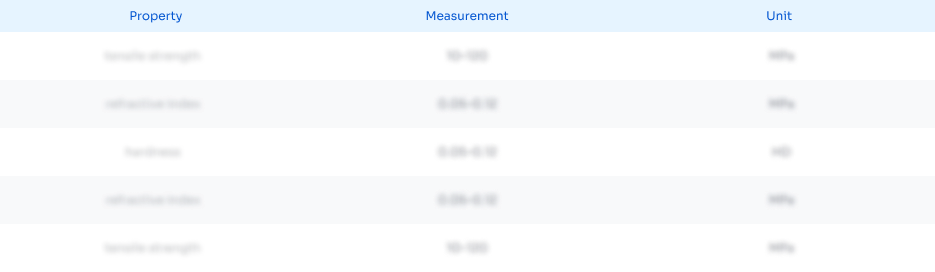
Abstract
Description
Claims
Application Information

- R&D
- Intellectual Property
- Life Sciences
- Materials
- Tech Scout
- Unparalleled Data Quality
- Higher Quality Content
- 60% Fewer Hallucinations
Browse by: Latest US Patents, China's latest patents, Technical Efficacy Thesaurus, Application Domain, Technology Topic, Popular Technical Reports.
© 2025 PatSnap. All rights reserved.Legal|Privacy policy|Modern Slavery Act Transparency Statement|Sitemap|About US| Contact US: help@patsnap.com