Calibration method for relative positions of three-dimensional sensor and mechanical arm
A technology of mechanical arm and calibration method, which is applied in the direction of instruments, measuring devices, optical devices, etc., can solve the problems of unreal-time feedback calibration accuracy, affecting the application efficiency of large-scale robots, and time-consuming and labor-intensive hand-eye calibration process.
- Summary
- Abstract
- Description
- Claims
- Application Information
AI Technical Summary
Problems solved by technology
Method used
Image
Examples
no. 1 example
[0031] see image 3 , the first embodiment of the present invention comprises the following steps:
[0032] S301. Move the end of the robotic arm to the field of view of the 3D sensor, so that the flange at the end faces the 3D sensor without obstruction, record the point cloud information of the flange acquired by the 3D sensor at this time, and extract the flange through a 3D vision algorithm At least one feature point of the disk, and obtain the three-dimensional coordinate value of the extracted feature point relative to the three-dimensional sensor coordinate system;
[0033] It should be noted that the feature points of the flange extracted in the above steps can be the center of the disc of the flange and / or the center of the threaded hole on the flange; when the selected feature points include the disc of the flange When the center and the center of the threaded hole on the flange, there are usually more than three feature points that can be selected, and these featur...
no. 2 example
[0039] see Figure 4 , the second embodiment of the present invention comprises the following steps:
[0040] S401. Move the end of the mechanical arm to the field of view of the three-dimensional sensor, so that the flange at the end faces the three-dimensional sensor without obstruction, record the point cloud information of the flange acquired by the three-dimensional sensor at this time, and extract the flange through a three-dimensional vision algorithm At least one feature point of the disk, and obtain the three-dimensional coordinate value of the extracted feature point relative to the three-dimensional sensor coordinate system and the normal vector of the flange;
[0041] It should be noted that the feature points of the flange extracted in the above steps can be the center of the disc of the flange and / or the center of the threaded hole on the flange; when the selected feature points include the disc of the flange When the center and the center of the threaded hole o...
no. 3 example
[0050] see Figure 5 , the third embodiment of the present invention comprises the following steps:
[0051] S501, move the end of the robotic arm to the field of view of the 3D sensor, and make the flange at the end face the 3D sensor without obstruction, record the point cloud information of the flange acquired by the 3D sensor at this time, and obtain it through the point cloud segmentation algorithm The point cloud image of the flange surface, and then the three-dimensional coordinate value of the center point of the flange disc in the three-dimensional sensor coordinate system and the normal vector of the flange are obtained through the circle fitting algorithm;
[0052] S502, read and record the position of the end of the robot arm relative to the base coordinate system of the robot arm from the controller of the robot arm, and obtain the three-dimensional coordinate value of the center point of the flange in the base coordinate system of the robot arm and the flange met...
PUM
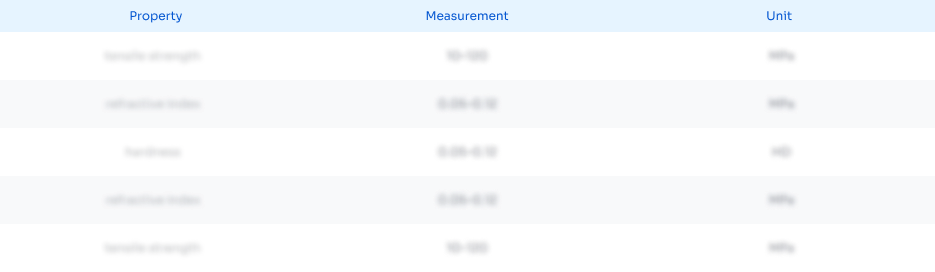
Abstract
Description
Claims
Application Information

- R&D
- Intellectual Property
- Life Sciences
- Materials
- Tech Scout
- Unparalleled Data Quality
- Higher Quality Content
- 60% Fewer Hallucinations
Browse by: Latest US Patents, China's latest patents, Technical Efficacy Thesaurus, Application Domain, Technology Topic, Popular Technical Reports.
© 2025 PatSnap. All rights reserved.Legal|Privacy policy|Modern Slavery Act Transparency Statement|Sitemap|About US| Contact US: help@patsnap.com