A kind of gas barrier degradable plastic masterbatch
A technology for degrading plastics and gas barriers, which is applied in the field of injection molding production and processing lines and conical twin-screw extruders. Strength and toughness, the effect of simple preparation steps
- Summary
- Abstract
- Description
- Claims
- Application Information
AI Technical Summary
Problems solved by technology
Method used
Image
Examples
Embodiment 1
[0060] Prepare gas-barrier biodegradable plastic masterbatches according to the following steps:
[0061] Step 1. Bamboo fiber modification: Take the bamboo fiber powder passed through a 100-mesh sieve and add it to the Pingpinga O-20 aqueous solution with a mass fraction of 0.1%, then add a 1% sodium hydroxide aqueous solution, and then heat it at 70°C Ultrasonic treatment (frequency 20KHz) for 50 minutes, placed in a drying oven at 50°C and dried until the water content is less than 2% to obtain modified bamboo fiber, bamboo fiber powder: Pingpingjia O aqueous solution: sodium hydroxide aqueous solution mass ratio It is 1:1:0.01.
[0062]Step 2: Add 4-6 parts of modified bamboo fiber obtained in step 1 to a high-speed mixer, then add 50 parts of polyhydroxyalkanoate PHA, 20 parts of polylactic acid PLA, 2.5 parts of feather powder, and 0.3 part of ring Oxygenated soybean oil, 0.4 part of dioctyl adipate, 0.7 part of glycidyl methacrylate GMA, 0.8 part of α-alkyl cyanoacryla...
Embodiment 2
[0064] Prepare gas-barrier biodegradable plastic masterbatches according to the following steps:
[0065] Step 1. Bamboo fiber modification: Take the bamboo fiber powder passed through a 200-mesh sieve and add it to the Pingpinga O aqueous solution with a mass fraction of 0.15%, then add a 2% sodium hydroxide aqueous solution, and then ultrasonicate at 60°C (Frequency 20KHz) Treat for 60 minutes, place in a drying oven at 60°C and dry until the water content is less than 2% to obtain modified bamboo fiber, bamboo fiber powder: Pingping O aqueous solution: sodium hydroxide aqueous solution mass ratio is 1 :1:0.02.
[0066] Step 2: Add 4-6 parts of modified bamboo fiber obtained in step 1 into a high-speed mixer, and then add 55 parts of polyhydroxyalkanoate PHA, 20 parts of polylactic acid PLA, 2 parts of feather powder, and 0.5 part of ring Oxygenated soybean oil, 0.2 part of dioctyl adipate, 0.5 part of glycidyl methacrylate GMA, 0.6 part of α-alkyl cyanoacrylate, 1.0 part o...
Embodiment 3
[0068] Prepare gas-barrier biodegradable plastic masterbatches according to the following steps:
[0069] Step 1. Bamboo fiber modification: Take the bamboo fiber powder passed through a 200-mesh sieve and add it to 0.1% Pingpinga O aqueous solution, then add 2% sodium hydroxide aqueous solution, and then ultrasonicate at 70°C (Frequency 20KHz) Treat for 80 minutes, place in a drying box and dry at a temperature lower than 60°C until the water content is less than 2% to obtain modified bamboo fiber, bamboo fiber powder: flat plus O aqueous solution: sodium hydroxide aqueous solution mass ratio It is 1:1:0.01.
[0070] Step 2: Add 4-6 parts of modified bamboo fiber obtained in step 1 to a high-speed mixer, and then add 51 parts of polyhydroxyalkanoate PHA, 18 parts of polylactic acid PLA, 3 parts of feather powder, and 0.5 part of ring Oxygenated soybean oil, 0.4 parts of dioctyl adipate, 0.7 parts of glycidyl methacrylate GMA, 0.7 parts of α-alkyl cyanoacrylate, 1.2 parts of ...
PUM
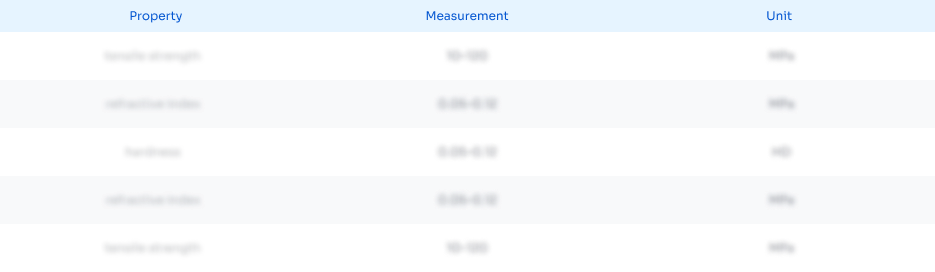
Abstract
Description
Claims
Application Information

- R&D
- Intellectual Property
- Life Sciences
- Materials
- Tech Scout
- Unparalleled Data Quality
- Higher Quality Content
- 60% Fewer Hallucinations
Browse by: Latest US Patents, China's latest patents, Technical Efficacy Thesaurus, Application Domain, Technology Topic, Popular Technical Reports.
© 2025 PatSnap. All rights reserved.Legal|Privacy policy|Modern Slavery Act Transparency Statement|Sitemap|About US| Contact US: help@patsnap.com