Forming method for film transfer of dry fiber fabric and application thereof
A fiber fabric and film transfer technology, applied in the field of composite materials, to achieve the effects of reducing deformation, ensuring molding quality, and improving adhesion
- Summary
- Abstract
- Description
- Claims
- Application Information
AI Technical Summary
Problems solved by technology
Method used
Image
Examples
Embodiment 1
[0053] Styling agent material: solution type setting agent Tack328 (solution type, solid content 17%)
[0054] Fabric type: G0827 unidirectional carbon fiber fabric, surface density 165g / m 2 , fiber type T300-3k.
[0055] The first step is to weigh Tack328 sizing agent at 29.1g per square meter (the solid content is equivalent to 3% of the weight of the G0827 fabric) and evenly spray it on the release paper. After the solvent evaporates, the sizing agent will form uniform spots on the release paper Shaped or flake-shaped adhesive film;
[0056] In the second step, the rolled G0827 unidirectional carbon fiber fabric is spread along the fiber direction on the release paper coated with a sizing agent, and the sizing agent film is transferred to the surface of the dry fiber fabric through a certain contact pressure, and the fabric and the release paper Coil together and reserve;
[0057] The third step is to unfold the rolled G0827 unidirectional carbon fiber fabric that has be...
Embodiment 2
[0065] Styling agent material: bisphenol A epoxy resin and hexafluoropolyaryletherketone prepolymer (dry setting agent).
[0066] Solvent: a mixed solvent made of tetrahydrofuran and acetone at a weight ratio of 1:1.
[0067] Fabric type: G0827 unidirectional carbon fiber fabric, surface density 165g / m 2 , fiber type T300-3k.
[0068] In the first step, the dry setting agent (bisphenol A epoxy resin and hexafluoropolyaryletherketone prepolymer) is dissolved in a mixed solvent of tetrahydrofuran and acetone (weight ratio 1:1) to make a solid content of 30 % of the fixative solution.
[0069] In the second step, weigh the sizing agent solution according to the solid content equivalent to 1% of the weight of the G0827 fabric, and evenly brush it on the release paper. After the solvent evaporates, the sizing agent will form uniform dots or flakes on the release paper Adhesive film;
[0070] The third step is to spread the roll of G0827 unidirectional carbon fiber fabric on the...
Embodiment 3
[0078] Embodiment 3 (existing shaping method)
[0079] Styling agent material: solution type setting agent Tack328 (solution type, solid content 17%)
[0080] Fabric type: G0827 unidirectional carbon fiber fabric, surface density 165g / m 2 , fiber type T300-3k.
[0081] The first step is to roll out the roll of G0827 unidirectional carbon fiber fabric, weigh Tack328 sizing agent (solid content is equivalent to 6% of the weight of G0827 fabric) at 58.2 per square meter, and directly spray the sizing agent on the fiber;
[0082] The second step is to cut the fabric into 13 pieces of 300mm×300mm in size after the setting agent solvent evaporates;
[0083] The third step is to lay 13 layers of fabric layer by layer, and handle with care to avoid fiber deformation.
[0084] See Example 1 and Example 2 for the preparation method of the preform of the present invention, and Example 3 for the method for preparing the preform in the prior art.
[0085] Put the preforms prepared by t...
PUM
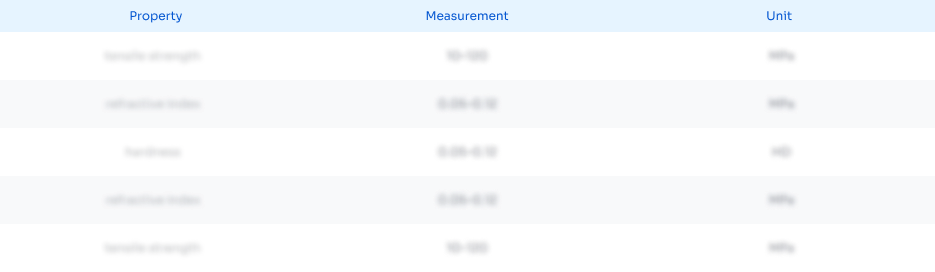
Abstract
Description
Claims
Application Information

- R&D
- Intellectual Property
- Life Sciences
- Materials
- Tech Scout
- Unparalleled Data Quality
- Higher Quality Content
- 60% Fewer Hallucinations
Browse by: Latest US Patents, China's latest patents, Technical Efficacy Thesaurus, Application Domain, Technology Topic, Popular Technical Reports.
© 2025 PatSnap. All rights reserved.Legal|Privacy policy|Modern Slavery Act Transparency Statement|Sitemap|About US| Contact US: help@patsnap.com