Ultrasonic control circuit triggered by position and pressure and welding method
A control circuit and ultrasonic technology, applied in welding equipment, non-electric welding equipment, manufacturing tools, etc., can solve problems such as welding failure and difficulty in starting the vibration of the ultrasonic generator, so as to ensure consistency, facilitate tracking and feedback control, and reduce welding The effect of bad rate
- Summary
- Abstract
- Description
- Claims
- Application Information
AI Technical Summary
Problems solved by technology
Method used
Image
Examples
Embodiment Construction
[0040] The principles and features of the present invention are described below in conjunction with the accompanying drawings, and the examples given are only used to explain the present invention, and are not intended to limit the scope of the present invention.
[0041] like figure 1 As shown, an ultrasonic control circuit triggered by position and pressure includes a sensing detection circuit, a sampling circuit, a main control circuit, an interface circuit, a driving circuit and a power supply, the sensing detection circuit is electrically connected to the sampling circuit, The sampling circuit, the interface circuit and the driving circuit are respectively electrically connected to the main control circuit, the driving circuit and the interface circuit are respectively electrically connected to the ultrasonic generator, and the power supply is respectively connected to the sensing detection circuit, the sampling circuit, the The main control circuit, the interface circuit...
PUM
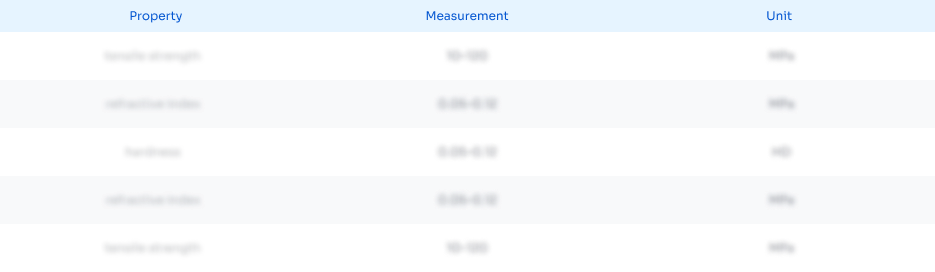
Abstract
Description
Claims
Application Information

- Generate Ideas
- Intellectual Property
- Life Sciences
- Materials
- Tech Scout
- Unparalleled Data Quality
- Higher Quality Content
- 60% Fewer Hallucinations
Browse by: Latest US Patents, China's latest patents, Technical Efficacy Thesaurus, Application Domain, Technology Topic, Popular Technical Reports.
© 2025 PatSnap. All rights reserved.Legal|Privacy policy|Modern Slavery Act Transparency Statement|Sitemap|About US| Contact US: help@patsnap.com