Preparation method of corrosion-resistant self-healing coating on magnesium alloy surface based on calcium salt
A magnesium alloy, self-repairing technology, applied in the direction of surface reaction electrolytic coating, metal material coating process, coating, etc., can solve the problems of limited corrosion protection and poor corrosion resistance, and achieve low equipment requirements, thickness and The effect of uniform structure and easy mass production
- Summary
- Abstract
- Description
- Claims
- Application Information
AI Technical Summary
Problems solved by technology
Method used
Image
Examples
preparation example Construction
[0026] A kind of preparation method of self-healing coating provided by the present invention, such as Figures 1 to 2 As shown, an oxide layer was prepared by micro-arc oxidation on the surface of the magnesium alloy using an electrolyte, and then a self-healing layer was prepared in an acidic solution containing calcium salts and corrosion inhibitors. Compared with the prior art, the self-healing layer provided by the present invention has a better protective effect in a corrosive environment, and has the following advantages as a workpiece: (a) a denser film layer and lower porosity; (b ) is loaded with corrosion inhibitor in the film layer, and the corrosion inhibitor can gather in the corrosion place in time when corrosion occurs, the self-repair method is sensitive, and the repair can be started in time; (c) multiple repairs in one area and simultaneous repairs in multiple areas can be realized, and automatic The repair method is sensitive, and the repair is started in t...
Embodiment 1
[0037] In this example, it is made by micro-arc oxidation and deposition in an acidic solution containing calcium salt and corrosion inhibitor on the surface of magnesium alloy using electrolyte solution. Follow the steps below to implement:
[0038] Step 1: Select AM50 magnesium alloy as the base material, and configure the micro-arc oxidation growth electrolyte composition: sodium silicate 20g / L, potassium fluoride 4g / L, and sodium hydroxide to adjust the pH value to 12;
[0039] Step 2: Use the metal substrate on which the oxide film needs to grow as the anode, and the graphite plate as the cathode, and adjust the distance between the cathode and anode to be 200mm;
[0040] Step 3: Select the constant current mode, the current density is 2A / dm 2 , the regulation pulse frequency is 300Hz, and the pulse duty cycle is 30%;
[0041] Step 4: Prepare the acidic calcium salt solution with the following components: calcium nitrate 30g / L, barbituric acid 0.01mol / L, nitric acid to ...
Embodiment 2
[0043]In this example, it is made by micro-arc oxidation and deposition in an acidic solution containing calcium salt and corrosion inhibitor on the surface of magnesium alloy using electrolyte solution. Follow the steps below to implement:
[0044] Step 1: Select AM50 magnesium alloy as the base material, and configure the micro-arc oxidation growth electrolyte composition: sodium silicate 20g / L, potassium fluoride 4g / L, and sodium hydroxide to adjust the pH value to 12;
[0045] Step 2: Use the metal substrate on which the oxide film needs to grow as the anode, and the graphite plate as the cathode, and adjust the distance between the cathode and anode to be 200mm;
[0046] Step 3: Select the constant voltage mode, the voltage value is 450V, the regulation pulse frequency is 300Hz, and the pulse duty cycle is 30%;
[0047] Step 4: Prepare the acidic calcium salt solution with the following components: calcium nitrate 30g / L, barbituric acid 0.01mol / L, nitric acid to adjust t...
PUM
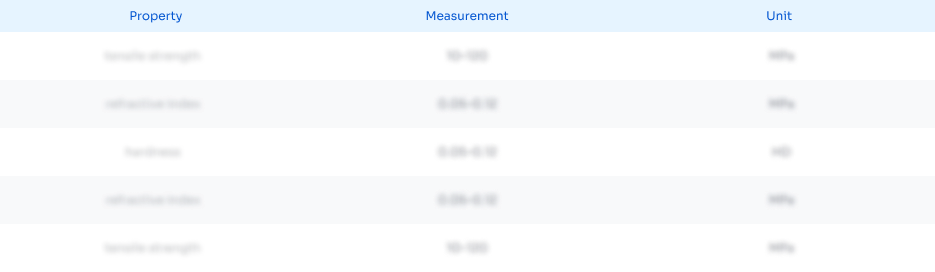
Abstract
Description
Claims
Application Information

- R&D
- Intellectual Property
- Life Sciences
- Materials
- Tech Scout
- Unparalleled Data Quality
- Higher Quality Content
- 60% Fewer Hallucinations
Browse by: Latest US Patents, China's latest patents, Technical Efficacy Thesaurus, Application Domain, Technology Topic, Popular Technical Reports.
© 2025 PatSnap. All rights reserved.Legal|Privacy policy|Modern Slavery Act Transparency Statement|Sitemap|About US| Contact US: help@patsnap.com