Assembly connection structure and assembly connection construction method of fabricated shear wall structure
A technology for connecting structures and shear walls, which is applied in the direction of walls, building components, and building structures, can solve problems such as the difficulty of walls and grouting channels, affecting the connection performance of walls, and difficult control of construction quality, and achieves easy Positioning and manufacturing accuracy, enhanced connection reliability, and superior seismic performance
- Summary
- Abstract
- Description
- Claims
- Application Information
AI Technical Summary
Problems solved by technology
Method used
Image
Examples
Embodiment Construction
[0041] It should be noted that all directional indications (such as up, down, left, right, front, back...) in the embodiments of the present invention are only used to explain the relationship between the components in a certain posture (as shown in the accompanying drawings). Relative positional relationship, movement conditions, etc., if the specific posture changes, the directional indication will also change accordingly.
[0042] Such as Figure 1 to Figure 9 As shown, the present invention provides an assembly connection structure of a prefabricated shear wall structure, comprising a shear wall 1, a section steel keel 2, a damping device 5, a bottom connection steel mold 3 and a top connection steel mold 4, horizontally to be connected The joints of the left and right shear walls 1 are pre-embedded with shaped steel keels 2, and the shaped steel keels 2 of the two shear walls 1 are connected by a damping device 5, and the joints of the upper and lower shear walls 1 to be ...
PUM
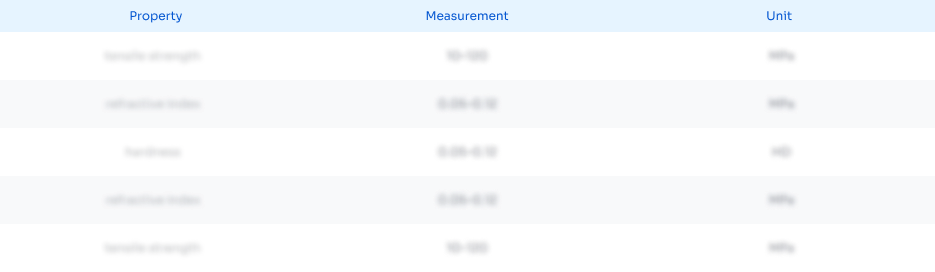
Abstract
Description
Claims
Application Information

- Generate Ideas
- Intellectual Property
- Life Sciences
- Materials
- Tech Scout
- Unparalleled Data Quality
- Higher Quality Content
- 60% Fewer Hallucinations
Browse by: Latest US Patents, China's latest patents, Technical Efficacy Thesaurus, Application Domain, Technology Topic, Popular Technical Reports.
© 2025 PatSnap. All rights reserved.Legal|Privacy policy|Modern Slavery Act Transparency Statement|Sitemap|About US| Contact US: help@patsnap.com