Method and system for measuring pose of industrial mechanical arm
A technology of engineering machinery and mechanical arms, which is applied in the field of measuring the pose and posture of engineering mechanical arms, and can solve the problems of prone to flexible deformation, large precise positioning of terminal operating devices, and long arm frame of multifunctional operating trolleys.
- Summary
- Abstract
- Description
- Claims
- Application Information
AI Technical Summary
Problems solved by technology
Method used
Image
Examples
Embodiment 1
[0028] First, introduce the following measurement tools used in this example: laser tracker (an example of a coordinate information collector), a foldable target ball mechanism (an example of a target, the specific structure can be as follows Figure 4 shown). The foldable target ball mechanism can be expanded and closed by the drive of the motor, so as to prevent the target ball from being blocked due to the movement of the mechanical arm during the measurement process and ensure the normal progress of the measurement. The structure of the target ball mechanism is not limited here, as long as the target ball can have the above functions.
[0029] Such as Figure 4 As shown, the meaning of each reference sign in the accompanying drawings is as follows: the meaning of each reference sign in the accompanying drawings is as follows: 1, base, 2, foldable target ball, 3, protective plate, 10, target ball support card Seat, 11, protective plate support deck, 12, middle drive frame...
Embodiment 2
[0081] Figure 7 It is the system for measuring the pose and posture of the engineering mechanical arm according to the second embodiment of the present application, and the following reference Figure 7 To illustrate the composition and function of the system.
[0082] like Figure 7 As shown, the system includes: at least three targets (illustrated B, C, D), which are installed at the end of the engineering mechanical arm, so that the at least three targets are in the middle of the mechanical arm frame The set point of the axis constitutes a predetermined position relationship; the parameter acquisition device 81, which acquires the position information of the at least three targets in the coordinate system of the robot arm carrier (the position coordinates are mainly measured by a laser tracker) and the The structural dimension parameters and installation dimension parameters of the target; the pose calculation device 82 at the end of the mechanical arm, which uses the pr...
PUM
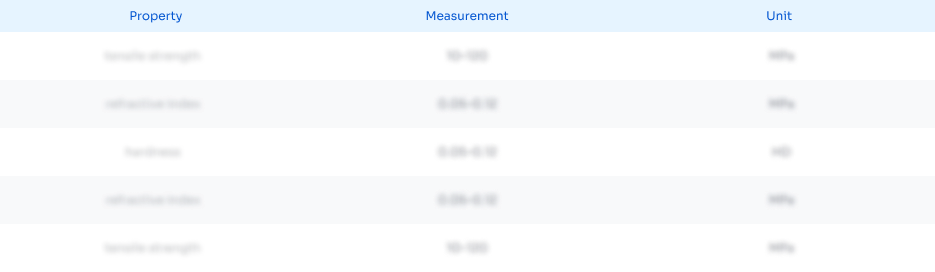
Abstract
Description
Claims
Application Information

- R&D Engineer
- R&D Manager
- IP Professional
- Industry Leading Data Capabilities
- Powerful AI technology
- Patent DNA Extraction
Browse by: Latest US Patents, China's latest patents, Technical Efficacy Thesaurus, Application Domain, Technology Topic, Popular Technical Reports.
© 2024 PatSnap. All rights reserved.Legal|Privacy policy|Modern Slavery Act Transparency Statement|Sitemap|About US| Contact US: help@patsnap.com