Control moment gyroscope
A technology for controlling torque gyroscopes and torque motors, which is applied in non-electric variable control, control/regulation systems, torque/mechanical power control, etc., can solve problems that cannot meet the high pointing accuracy and light weight of agile satellites, and the low precision of resolvers , heavy weight and other issues, to achieve high-precision position output, avoid magnetic interference, and light weight
- Summary
- Abstract
- Description
- Claims
- Application Information
AI Technical Summary
Problems solved by technology
Method used
Image
Examples
Embodiment Construction
[0020] The present invention will be further elaborated below by describing a preferred specific embodiment in detail in conjunction with the accompanying drawings.
[0021] Such as figure 1 As shown, a control torque gyroscope provided in this embodiment includes: a momentum wheel 10, an outer frame system 20, a torque motor 30 and a photoelectric encoder 40. In this embodiment, the photoelectric encoder 40 is an absolute photoelectric encoder Encoder.
[0022] The outer frame system 20 includes an outer frame 200, a driving end supporting frame 201 and a sensing end supporting frame 201' respectively fixed on both sides of the outer frame 200, a precision bearing 202, a driving end main shaft 203 and a sensing end main shaft 204 , the driving end main shaft 203 is installed on the driving end supporting frame 201 through the precision bearing 202 , and the sensing end main shaft 204 is installed on the sensing end supporting frame 201 ′ through the precision bearing 202 . ...
PUM
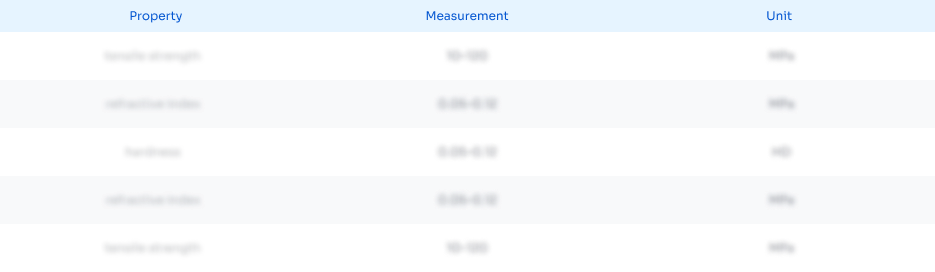
Abstract
Description
Claims
Application Information

- Generate Ideas
- Intellectual Property
- Life Sciences
- Materials
- Tech Scout
- Unparalleled Data Quality
- Higher Quality Content
- 60% Fewer Hallucinations
Browse by: Latest US Patents, China's latest patents, Technical Efficacy Thesaurus, Application Domain, Technology Topic, Popular Technical Reports.
© 2025 PatSnap. All rights reserved.Legal|Privacy policy|Modern Slavery Act Transparency Statement|Sitemap|About US| Contact US: help@patsnap.com