Control moment gyro driven by parallel type linear ultrasonic motor
A technology for controlling torque gyroscopes and ultrasonic motors, applied to rotating gyroscopes, etc., can solve the problems of complex locking mechanism, poor control accuracy, and slow response, and achieve high response, rapid action, and long service life.
- Summary
- Abstract
- Description
- Claims
- Application Information
AI Technical Summary
Problems solved by technology
Method used
Image
Examples
Embodiment Construction
[0033] In order to make the object, technical solution and effect of the present invention clearer and clearer, the present invention will be further described in detail below with reference to the accompanying drawings and examples. It should be pointed out that the specific implementations described here are only used to explain the present invention, not to limit the present invention.
[0034] Such as Figure 1~2 As shown, the present invention includes a rotating assembly, a fixed assembly, and a fixed assembly. The moment gyroscope is integrally divided into a two-stage structure, the upper end part is a rotating assembly, and the lower end part is a fixed assembly.
[0035] The rotating assembly includes a momentum wheel protection housing 15, and the momentum wheel protection housing 15 includes a momentum wheel 1, a high-speed motor 2, and a first angle encoder 3; the momentum wheel 1 is connected to the high-speed motor 2 stator or is formed by the momentum wheel 1 ...
PUM
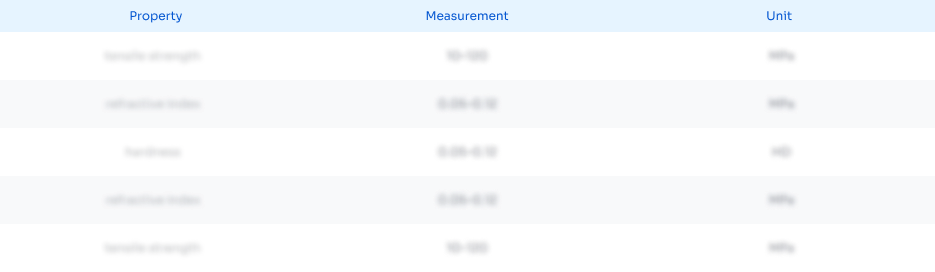
Abstract
Description
Claims
Application Information

- R&D
- Intellectual Property
- Life Sciences
- Materials
- Tech Scout
- Unparalleled Data Quality
- Higher Quality Content
- 60% Fewer Hallucinations
Browse by: Latest US Patents, China's latest patents, Technical Efficacy Thesaurus, Application Domain, Technology Topic, Popular Technical Reports.
© 2025 PatSnap. All rights reserved.Legal|Privacy policy|Modern Slavery Act Transparency Statement|Sitemap|About US| Contact US: help@patsnap.com