Shaping delayed treatment technology for materials in filling area in additive manufacturing
An additive manufacturing and process technology, which is applied in the field of 3D printing and can solve problems such as sacrificing molding efficiency
- Summary
- Abstract
- Description
- Claims
- Application Information
AI Technical Summary
Problems solved by technology
Method used
Image
Examples
Embodiment Construction
[0015] The present invention will be described in further detail below in conjunction with the accompanying drawings.
[0016] Such as figure 2 As shown, the water cup SLA product is made of transparent material, the wall thickness of the model is 5mm, and the boundary (1) (shell) is set to be 0.5mm thick, so the thickness of the photosensitive resin (2) in the middle solid area is 5-0.5*2=4mm. Considering that the bottom of the water cup model and the boundary (1) of the handle are suspended in the air, additional support (3) structures are added for them in the boundary (1).
[0017] Boundary (1) and support inside the boundary (3) are stacked layer by layer according to the conventional SLA process. At the same time, during the layer-by-layer stacking of the boundary, the photosensitive resin (3) molding raw material remains within the boundary (1), naturally forming the filling of the internal solid area.
[0018] After the conventional SLA molding is completed, the pho...
PUM
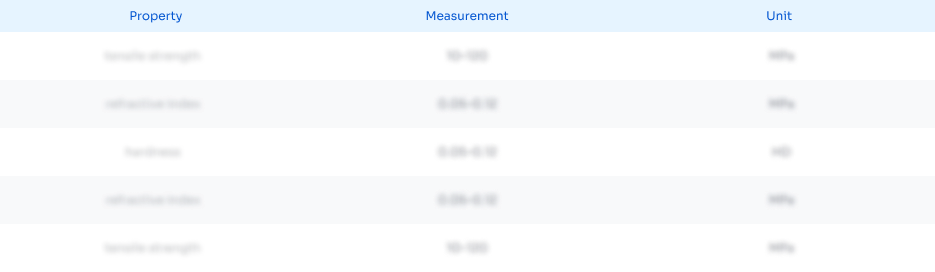
Abstract
Description
Claims
Application Information

- Generate Ideas
- Intellectual Property
- Life Sciences
- Materials
- Tech Scout
- Unparalleled Data Quality
- Higher Quality Content
- 60% Fewer Hallucinations
Browse by: Latest US Patents, China's latest patents, Technical Efficacy Thesaurus, Application Domain, Technology Topic, Popular Technical Reports.
© 2025 PatSnap. All rights reserved.Legal|Privacy policy|Modern Slavery Act Transparency Statement|Sitemap|About US| Contact US: help@patsnap.com