Vibration and noise reduction spring connected with multi-period structure in series
A vibration reduction and noise reduction, periodic structure technology, applied in springs, low internal friction springs, springs/shock absorbers, etc., can solve problems such as being difficult to withstand external forces, large temperature effects, and affecting aircraft vibration reduction and noise reduction. The effect of improving the life of the structure, improving the vibration damping performance, and isolating the transmission of vibration
- Summary
- Abstract
- Description
- Claims
- Application Information
AI Technical Summary
Problems solved by technology
Method used
Image
Examples
Embodiment Construction
[0024] In order to make the objectives, technical solutions and advantages of the present invention clearer, the technical solutions in the embodiments of the present invention will be described in more detail below in conjunction with the drawings in the embodiments of the present invention. What needs to be explained before this is that the terms or words used in this specification and claims should not be limited to be interpreted as the usual meaning or the meaning in the dictionary, but should be based on the best way for the inventor to explain his invention. The principle of appropriately defining the concepts of terms is interpreted as meanings and concepts consistent with the technical idea of the present invention. Subsequently, the embodiment described in this description and the structure shown in the drawings are only one of the best embodiments of the present invention, and cannot fully represent the technical ideas of the present invention, so it should be unde...
PUM
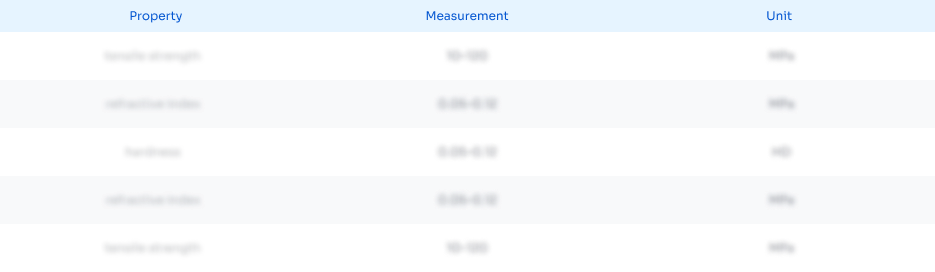
Abstract
Description
Claims
Application Information

- R&D
- Intellectual Property
- Life Sciences
- Materials
- Tech Scout
- Unparalleled Data Quality
- Higher Quality Content
- 60% Fewer Hallucinations
Browse by: Latest US Patents, China's latest patents, Technical Efficacy Thesaurus, Application Domain, Technology Topic, Popular Technical Reports.
© 2025 PatSnap. All rights reserved.Legal|Privacy policy|Modern Slavery Act Transparency Statement|Sitemap|About US| Contact US: help@patsnap.com