Method for preparing anti-aging coating for numerical-control machine tools
A technology of anti-aging coatings and preparation methods, which is applied in the direction of epoxy resin coatings, polyurea/polyurethane coatings, coatings, etc., to achieve good anti-aging effects and improve performance
- Summary
- Abstract
- Description
- Claims
- Application Information
AI Technical Summary
Problems solved by technology
Method used
Examples
Embodiment 1
[0012] The invention discloses a method for preparing an anti-aging coating for a numerically controlled machine tool. The components are as follows in parts by mass: 20 parts of an anti-aging coating base liquid and 30 parts of an anti-aging additive. After uniform mixing, the anti-aging coating can be obtained.
[0013] The anti-aging coating base liquid has the following components in parts by mass: 30 parts of epoxy resin and 40 parts of polyvinyl chloride resin are stirred and mixed, the stirring time is 1H, and the stirring temperature is 100 degrees, and then 20 parts of acrylic polyurethane is added. Stir continuously, the stirring time is 0.5H, the stirring temperature is 90°C, and the anti-aging coating base liquid is obtained after the stirring is completed.
[0014] The anti-aging additive has the following components in parts by mass: 2 parts of potassium methyl siliconate, 6 parts of o-hydroxybenzophenone and 1 part of o-hydroxybenzotriazole are mixed and stirred,...
Embodiment 2
[0016] A method for preparing an anti-aging coating for numerically controlled machine tools, characterized in that the components are as follows in parts by mass: 40 parts of anti-aging coating base liquid, 100 parts of anti-aging additives, and the anti-aging coating can be obtained after uniform mixing .
[0017] The anti-aging coating base liquid has the following components in parts by mass: 90 parts of epoxy resin and 60 parts of polyvinyl chloride resin are stirred and mixed, the stirring time is 2 hours, the stirring temperature is 100 degrees, and then 30 parts of acrylic polyurethane is added Stir continuously, the stirring time is 1.5H, and the stirring temperature is 90 degrees, and the anti-aging coating base liquid is obtained after the stirring is completed.
[0018] The anti-aging additive has the following components in parts by mass: 6 parts of potassium methyl siliconate, 10 parts of o-hydroxybenzophenone and 2 parts of o-hydroxybenzotriazole are mixed and s...
PUM
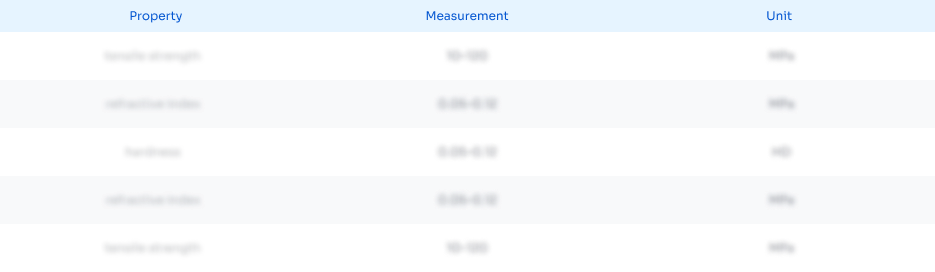
Abstract
Description
Claims
Application Information

- R&D Engineer
- R&D Manager
- IP Professional
- Industry Leading Data Capabilities
- Powerful AI technology
- Patent DNA Extraction
Browse by: Latest US Patents, China's latest patents, Technical Efficacy Thesaurus, Application Domain, Technology Topic, Popular Technical Reports.
© 2024 PatSnap. All rights reserved.Legal|Privacy policy|Modern Slavery Act Transparency Statement|Sitemap|About US| Contact US: help@patsnap.com