Automatic workpiece polishing method based on off-line programming
An offline programming and processing method technology, applied in the control of workpiece feed movement, grinding workpiece support, metal processing equipment, etc., can solve the problems of complex 3D data steps, increase the difficulty of grinding methods, and cannot guarantee the grinding effect, etc. The effect of ensuring uniformity and quality and reducing the difficulty of program design
- Summary
- Abstract
- Description
- Claims
- Application Information
AI Technical Summary
Problems solved by technology
Method used
Image
Examples
Embodiment Construction
[0029] Embodiments of the invention are described in detail below, but the invention can be practiced in many different ways as defined and covered by the claims.
[0030] A kind of workpiece automatic grinding processing method based on off-line programming provided by this embodiment, it comprises the following steps:
[0031] S1, import the 3D graphic file data of the workpiece to be processed (it can adopt the 3D graphic file format designed by three-dimensional software such as PROE, UG according to the actual situation) into the offline programming software, so as to utilize the offline programming software to generate reference grinding tracks;
[0032] S2. Select a workpiece that is consistent with the 3D image file model of the workpiece to be processed as the physical standard workpiece (wherein, the "conformity" mentioned can refer to that the physical standard workpiece is consistent with or approximate to the 3D image file model in data theory, and Physical standa...
PUM
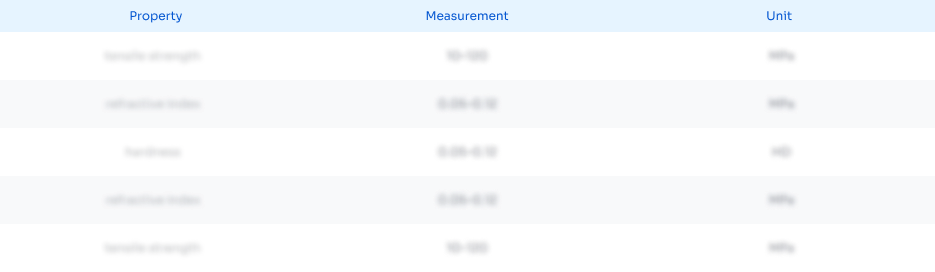
Abstract
Description
Claims
Application Information

- R&D Engineer
- R&D Manager
- IP Professional
- Industry Leading Data Capabilities
- Powerful AI technology
- Patent DNA Extraction
Browse by: Latest US Patents, China's latest patents, Technical Efficacy Thesaurus, Application Domain, Technology Topic, Popular Technical Reports.
© 2024 PatSnap. All rights reserved.Legal|Privacy policy|Modern Slavery Act Transparency Statement|Sitemap|About US| Contact US: help@patsnap.com