Furnace inner base plate for natural gas heating furnace
A heating furnace and natural gas technology, applied in the field of machinery and equipment, can solve the problems of production continuity and the reduction of the service life of the bottom refractory brick, and achieve the effects of increasing the service life, reducing friction and avoiding repair time.
- Summary
- Abstract
- Description
- Claims
- Application Information
AI Technical Summary
Problems solved by technology
Method used
Image
Examples
Embodiment 1
[0016] Embodiment 1: as figure 1 The shown backing plate for the natural gas heating furnace includes the backing plate 1 of HT10-26, and the backing plate 1 has a lower surface matched with the bottom surface of the furnace, and the backing plate 1 is sequentially It is a plane heating zone 2 and a downhill discharge zone 3, the plane heating zone 2 has a smooth upper surface, and the downhill discharge zone 3 has a slope angle of 3° along the direction from the inlet to the outlet. The upper surface is smooth, the length of the planar heating zone 2 is greater than the length of the downhill discharge zone 3, preferably with a length ratio of 1.6, and the backing plate 1 is laid on the bottom surface of the hearth of the heating furnace.
PUM
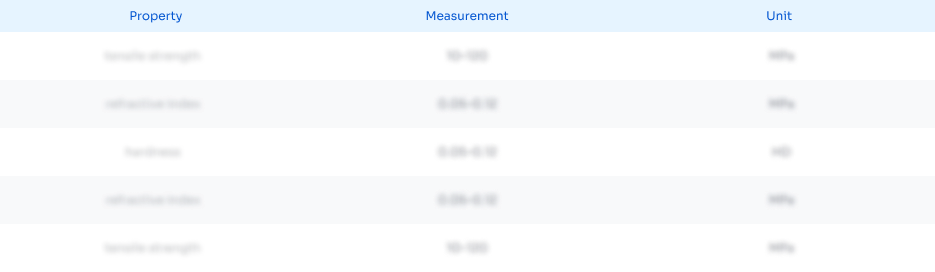
Abstract
Description
Claims
Application Information

- R&D Engineer
- R&D Manager
- IP Professional
- Industry Leading Data Capabilities
- Powerful AI technology
- Patent DNA Extraction
Browse by: Latest US Patents, China's latest patents, Technical Efficacy Thesaurus, Application Domain, Technology Topic, Popular Technical Reports.
© 2024 PatSnap. All rights reserved.Legal|Privacy policy|Modern Slavery Act Transparency Statement|Sitemap|About US| Contact US: help@patsnap.com