Metal deposition forming method and device based on ultra-high frequency induction heating technology
A technology of induction heating and induction heating power supply, which is applied in the field of additive manufacturing, can solve the problems of high cost and low forming efficiency, achieve low equipment cost, high thermal energy conversion rate, and realize the effect of precise melting deposition forming
- Summary
- Abstract
- Description
- Claims
- Application Information
AI Technical Summary
Problems solved by technology
Method used
Image
Examples
Embodiment Construction
[0023] Attached below Figure 1-2 The present invention will be further described with specific embodiments.
[0024] The present invention provides a metal deposition forming method based on ultra-high frequency induction heating. Based on the principle of ultra-high frequency induction heating, an ultra-high frequency alternating magnetic field is generated near the induction coil 2 by using an ultra-high frequency induction heating power supply 1, and the metal The wire material 4 is fed into the center of the induction coil 2, and the metal wire material 4 generates an induced eddy current inside it under the action of an alternating magnetic field, and the metal wire material 4 is melted by the heat effect of the induced eddy current, and piled up layer by layer to form a metal deposition molded part 5;
[0025] Among them, the frequency of the ultra-high frequency induction heating power supply 1 is 500-1100kHz, the output current is 5-30A, the wire feeding speed of the ...
PUM
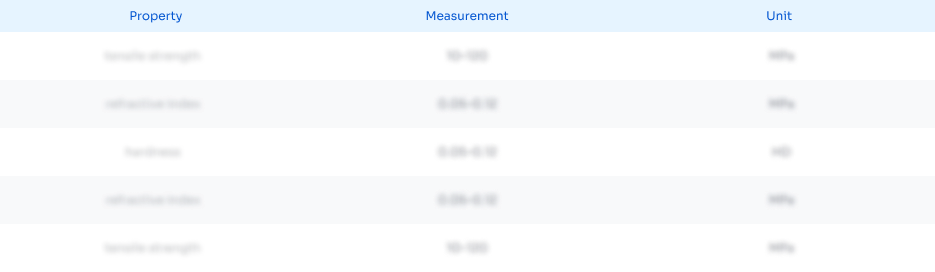
Abstract
Description
Claims
Application Information

- R&D Engineer
- R&D Manager
- IP Professional
- Industry Leading Data Capabilities
- Powerful AI technology
- Patent DNA Extraction
Browse by: Latest US Patents, China's latest patents, Technical Efficacy Thesaurus, Application Domain, Technology Topic, Popular Technical Reports.
© 2024 PatSnap. All rights reserved.Legal|Privacy policy|Modern Slavery Act Transparency Statement|Sitemap|About US| Contact US: help@patsnap.com