Polyphenylene sulfide resin synthesis process
A technology for polyphenylene sulfide resin and synthesis process is applied in the field of synthesis technology of polyphenylene sulfide resin, which can solve the problem of irregular polyphenylene sulfide resin particles, fine polyphenylene sulfide resin particles, and polyphenylene sulfide resin molding. Difficulties and other problems, to achieve the effect of omitting the treatment process, improving the particle forming rate, and reducing soluble by-products
- Summary
- Abstract
- Description
- Claims
- Application Information
AI Technical Summary
Problems solved by technology
Method used
Examples
Embodiment 1
[0030] The synthesis process of polyphenylene sulfide resin:
[0031] (1) Under the condition of nitrogen protection, add sodium hydrogen sulfide and oxygen-free deionized water into one reaction kettle to form an aqueous solution containing 45%wt of sodium hydrogen sulfide, and in another reaction kettle, under the condition of nitrogen protection Next, add sodium hydroxide and oxygen-free deionized water to form an aqueous solution containing 45%wt of sodium hydroxide, then heat the materials in the two reactors to 80°C, and use an alkali-resistant pump to input the aqueous sodium hydroxide solution into the container. In a reaction kettle with sodium hydrosulfide dissolved in water, when the material temperature reaches 120°C, under this temperature condition, after 30 minutes of heat preservation to generate sodium sulfide, N-methylpyrrolidone is added to make Na 2 The molar ratio of S:NMP is 1.0:3.8, the temperature of the material in the reactor is raised to 200°C at a t...
Embodiment 2
[0039] The synthesis process of polyphenylene sulfide resin:
[0040] (1) Under the condition of nitrogen protection, add sodium hydrogen sulfide and oxygen-free deionized water into one reaction kettle to form an aqueous solution containing 60%wt of sodium hydrogen sulfide, and in another reaction kettle, under the condition of nitrogen protection Next, add sodium hydroxide and oxygen-free deionized water to form an aqueous solution containing 60%wt of sodium hydroxide, then heat the materials in the two reactors to 100°C, and use an alkali-resistant pump to input the aqueous solution of sodium hydroxide into the container. In a reaction kettle with sodium hydrosulfide dissolved in water, when the temperature of the material reaches 130°C, under this temperature condition, after 18 minutes of heat preservation to generate sodium sulfide, N-methylpyrrolidone is added to make Na 2 The molar ratio of S:NMP is 1.0:5.8, the temperature of the material in the reactor is raised to 2...
Embodiment 3
[0048] The synthesis process of polyphenylene sulfide resin:
[0049] (1) Under the condition of nitrogen protection, add sodium hydrogen sulfide and oxygen-free deionized water into one reaction kettle to form an aqueous solution containing 48%wt of sodium hydrogen sulfide, and in another reaction kettle, under the condition of nitrogen protection Next, add sodium hydroxide and oxygen-free deionized water to form an aqueous solution containing 52%wt of sodium hydroxide, then heat the materials in the two reactors to 83°C, and use an alkali-resistant pump to input the aqueous sodium hydroxide solution into the container. In a reaction kettle with sodium hydrosulfide dissolved in water, when the temperature of the material reaches 123°C, under this temperature condition, after 21 minutes of heat preservation to generate sodium sulfide, N-methylpyrrolidone is added to make Na2 The molar ratio of S:NMP is 1.0:4.3, and the temperature of the material in the reactor is raised to 203...
PUM
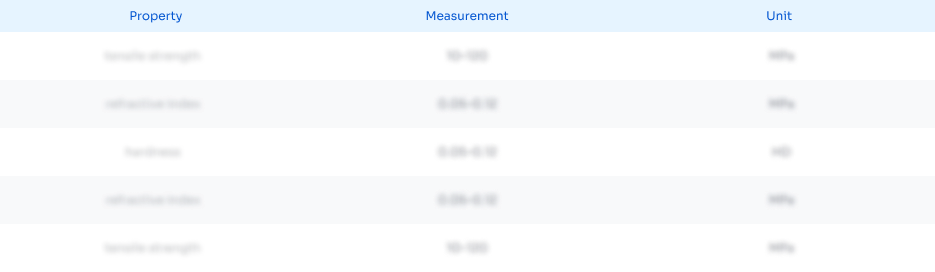
Abstract
Description
Claims
Application Information

- R&D
- Intellectual Property
- Life Sciences
- Materials
- Tech Scout
- Unparalleled Data Quality
- Higher Quality Content
- 60% Fewer Hallucinations
Browse by: Latest US Patents, China's latest patents, Technical Efficacy Thesaurus, Application Domain, Technology Topic, Popular Technical Reports.
© 2025 PatSnap. All rights reserved.Legal|Privacy policy|Modern Slavery Act Transparency Statement|Sitemap|About US| Contact US: help@patsnap.com