A self-adaptive grinding device for the inner wall of a polyurethane-coated cylinder
A self-adaptive, inner wall surface technology, which is applied in the direction of grinding/polishing safety devices, grinding machines, grinding/polishing equipment, etc., can solve the problems of high labor intensity for grinding technicians, too tight or too loose filling of the coating cylinder, and It is difficult to fit the cylinder into the mold and other problems, so as to achieve the effect of controllable product consistency, continuous long-term grinding, and saving grinding time
- Summary
- Abstract
- Description
- Claims
- Application Information
AI Technical Summary
Problems solved by technology
Method used
Image
Examples
Embodiment Construction
[0016] The present invention will be further described below in conjunction with the accompanying drawings and specific embodiments.
[0017] Such as figure 1 and figure 2 As shown in the figure, a self-adaptive grinding device for the inner wall of a polyurethane-coated cylinder includes an automatic loading and unloading mechanism 1, an automatic clamping mechanism 2, an automatic grinding mechanism 3, a dust recovery system 4, and a closed casing 5, wherein the automatic clamping mechanism 2 , The automatic grinding mechanism 3 is sealed inside the closed casing 5 .
[0018] Such as image 3 As shown, the automatic loading and unloading mechanism 1 includes a silo 11, a feeding port 12, a pneumatic expansion shaft 13, and a two-dimensional guide rail 14. The silo 11 is installed obliquely. Under the action of gravity, it slides along the wall surface of the feed bin 11 to the feeding port 12, and the feeding port 12 is opened at the bottom of the feeding bin 11. In the...
PUM
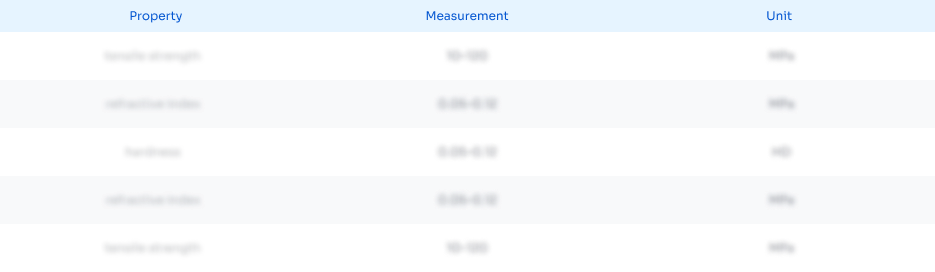
Abstract
Description
Claims
Application Information

- R&D
- Intellectual Property
- Life Sciences
- Materials
- Tech Scout
- Unparalleled Data Quality
- Higher Quality Content
- 60% Fewer Hallucinations
Browse by: Latest US Patents, China's latest patents, Technical Efficacy Thesaurus, Application Domain, Technology Topic, Popular Technical Reports.
© 2025 PatSnap. All rights reserved.Legal|Privacy policy|Modern Slavery Act Transparency Statement|Sitemap|About US| Contact US: help@patsnap.com