Control system and method of co-fusion robot for optical mirror surface machining
A technology of optical mirror surface and control system, which is applied in general control system, control/adjustment system, digital control, etc. It can solve the problems of difficult control module, inability to judge in advance, and difficulty in meeting high-precision mirror processing requirements, so as to improve processing accuracy Effect
- Summary
- Abstract
- Description
- Claims
- Application Information
AI Technical Summary
Problems solved by technology
Method used
Image
Examples
Embodiment Construction
[0024] The present invention will be described in detail below in conjunction with the accompanying drawings and specific embodiments.
[0025] Such as figure 1As shown, a fusion robot control system for optical mirror surface processing includes a moving platform driving unit, a tool holder driving unit, a flexible hydraulic support unit and a rotating platform control unit. The moving platform driving unit is used to drive the movement of the moving platform, and the tool holder drives The unit is used to drive the action of the tool holder, the flexible hydraulic support unit is used to support the optical mirror, and the rotating platform control unit is used to control the rotation of the optical mirror around the Z axis; it also includes an intelligent control system, a visual inspection module, and a high-precision three-coordinate inspection machine , multi-axis motion controller and processing platform controller, the output end of the multi-axis motion controller is ...
PUM
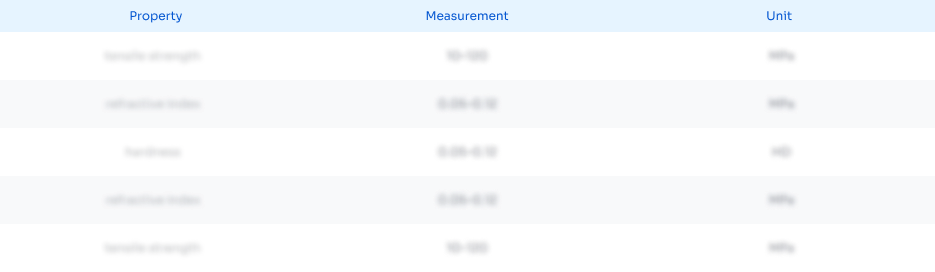
Abstract
Description
Claims
Application Information

- Generate Ideas
- Intellectual Property
- Life Sciences
- Materials
- Tech Scout
- Unparalleled Data Quality
- Higher Quality Content
- 60% Fewer Hallucinations
Browse by: Latest US Patents, China's latest patents, Technical Efficacy Thesaurus, Application Domain, Technology Topic, Popular Technical Reports.
© 2025 PatSnap. All rights reserved.Legal|Privacy policy|Modern Slavery Act Transparency Statement|Sitemap|About US| Contact US: help@patsnap.com