Lens position adjusting mechanism for optical system
A technology for adjusting mechanisms and optical systems, applied in optics, optical components, installation, etc., can solve problems that are difficult to meet, difficult to clean, and easily damaged optical systems, and achieve the effects of simple adjustment operations, accurate relative positions, and guaranteed stability
- Summary
- Abstract
- Description
- Claims
- Application Information
AI Technical Summary
Problems solved by technology
Method used
Image
Examples
Embodiment Construction
[0029] The present invention will be further described in detail below in conjunction with the accompanying drawings and specific embodiments to facilitate a clear understanding of the present invention, but they do not limit the present invention.
[0030] like Figure 2-5 Shown, the present invention comprises objective lens 1, the flat lens holder 4 of fixed flat lens 7, the axicon lens holder 6 of fixed axicon lens 8, outer sleeve 3 and axicon lens adjustment sleeve 5, described objective lens 1, flat lens 7 and the axicon lens 8 are coaxially arranged in turn; one end of the outer sleeve 3 is connected to the axial limit of the end of the objective lens 1, the inner wall of the outer sleeve 3 is threaded with the outer wall of the flat lens holder 4, and the flat lens holder 4 A first cavity 39 is provided between one end and the objective lens 1, the other end of the flat lens holder 4 is fixedly connected with one end of the axicon lens adjustment sleeve 5, the inner wa...
PUM
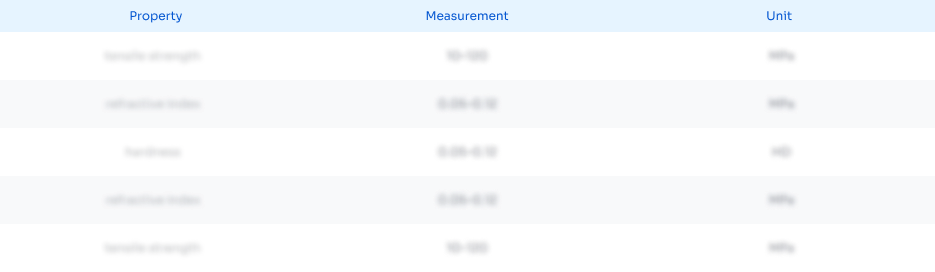
Abstract
Description
Claims
Application Information

- R&D Engineer
- R&D Manager
- IP Professional
- Industry Leading Data Capabilities
- Powerful AI technology
- Patent DNA Extraction
Browse by: Latest US Patents, China's latest patents, Technical Efficacy Thesaurus, Application Domain, Technology Topic, Popular Technical Reports.
© 2024 PatSnap. All rights reserved.Legal|Privacy policy|Modern Slavery Act Transparency Statement|Sitemap|About US| Contact US: help@patsnap.com