Composite flame-retardant heat-insulation material for exterior walls and method for preparing composite flame-retardant heat-insulation material
A technology of composite flame retardant and thermal insulation materials, applied in the field of building materials, can solve the problems of questioning the fire performance of organic thermal insulation materials, restricting the application of urea-formaldehyde resin, poor water resistance, etc.
- Summary
- Abstract
- Description
- Claims
- Application Information
AI Technical Summary
Problems solved by technology
Method used
Image
Examples
Embodiment 1
[0023] The present embodiment provides a composite flame-retardant thermal insulation material for exterior walls, and the specific manufacturing steps are as follows:
[0024] 1. Preparation of urea-formaldehyde resin, including the following steps:
[0025] (1) Dissolving of polyvinyl alcohol: Add 100 parts of formaldehyde and 0.1 part of polyvinyl alcohol PVA in turn to the three-necked flask equipped with an electric stirring device, a reflux condensing device and a temperature measuring device until the polyvinyl alcohol PVA is completely dissolved.
[0026] (2) Weighing urea: Weighing 0.65 part of urea, the urea that will be weighed will be divided into 3 parts, respectively accounting for 60% of the total amount of urea or 0.39 part, 30% or 0.195 part of urea and 10% or 0.065 part of urea .
[0027] (3) Add urea: turn on the stirring device, adjust the stirring speed to be 100r / min, add 0.39 part of urea while stirring, adjust the pH value to 7.0 after the urea is comp...
Embodiment 2
[0033] The present embodiment provides a composite flame-retardant thermal insulation material for exterior walls, and the specific manufacturing steps are as follows:
[0034] 1. Preparation of urea-formaldehyde resin, including the following steps:
[0035] (1) Dissolving of polyvinyl alcohol: Add 100 parts of formaldehyde and 1.5 parts of polyvinyl alcohol PVA successively to the three-necked flask equipped with an electric stirring device, a reflux condensing device and a temperature measuring device, until the polyvinyl alcohol PVA is completely dissolved.
[0036] (2) take urea by weighing: take 0.8 part of urea, divide the urea that will be weighed into 3 parts, respectively account for 60% of the total amount of urea, namely 0.48 part of urea, 30% or 0.24 part of urea and 10% or 0.08 part of urea urea.
[0037] (3) Add urea: open the stirring device, adjust the stirring speed to 100r / min, add 0.48 part of urea while stirring, adjust the pH value to 7.0 after the urea ...
Embodiment 3
[0043] The present embodiment provides a composite flame-retardant thermal insulation material for exterior walls, and the specific manufacturing steps are as follows:
[0044] 1. Preparation of urea-formaldehyde resin, including the following steps:
[0045] (1) Dissolving of polyvinyl alcohol: Add 100 parts of formaldehyde and 3 parts of polyvinyl alcohol PVA successively to the three-necked flask equipped with an electric stirring device, a reflux condensing device and a temperature measuring device until the polyvinyl alcohol PVA is completely dissolved.
[0046] (2) Weighing urea: Weighing 0.95 part of urea, the urea that will be weighed will be divided into 3 parts, respectively accounting for 60% of the total amount of urea or 0.57 part of urea, 30% or 0.285 part of urea and 10% or 0.095 part of urea urea.
[0047] (3) Add urea: turn on the stirring device, adjust the stirring speed to 100r / min, add 0.57 part of urea while stirring, adjust the pH value to 8.0 after the...
PUM
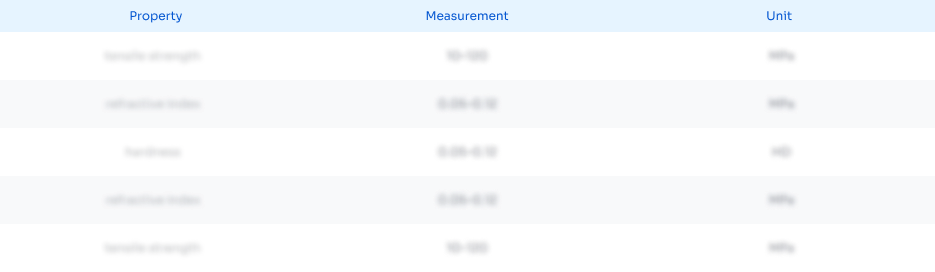
Abstract
Description
Claims
Application Information

- R&D
- Intellectual Property
- Life Sciences
- Materials
- Tech Scout
- Unparalleled Data Quality
- Higher Quality Content
- 60% Fewer Hallucinations
Browse by: Latest US Patents, China's latest patents, Technical Efficacy Thesaurus, Application Domain, Technology Topic, Popular Technical Reports.
© 2025 PatSnap. All rights reserved.Legal|Privacy policy|Modern Slavery Act Transparency Statement|Sitemap|About US| Contact US: help@patsnap.com