Section bar cast-rolling method and system based on horizontal cast-rolling mill
A casting and rolling machine, horizontal technology, applied in the field of profile casting and rolling system based on horizontal casting and rolling machine, can solve the problems of fragile casting and rolling system, low production efficiency, limited application range, etc., to ensure uniformity and uniform cooling Effect
- Summary
- Abstract
- Description
- Claims
- Application Information
AI Technical Summary
Problems solved by technology
Method used
Image
Examples
Embodiment 1
[0065] Embodiment 1: as Figure 1~4 , a profile casting and rolling system based on a horizontal casting and rolling machine, including a melting furnace, a front box, a distribution mechanism and a casting and rolling mechanism;
[0066] The melting furnace is connected to the front box through a connecting mechanism (such as a pipe, a trough component, etc.), and the melt in the melting furnace enters the front box through the connecting mechanism;
[0067] The melt in the front box flows into the casting and rolling mechanism through the distribution mechanism;
[0068] The casting-rolling mechanism includes an upper roll 1 and a lower roll 2; the axes of the upper roll and the lower roll are parallel and located in the same vertical plane; the roll surface of the upper roll or the lower roll is provided with a cavity; , the upper roll and the lower roll rotate under the drive of the driving mechanism; the rotation direction of the upper roll and the lower roll is opposite...
PUM
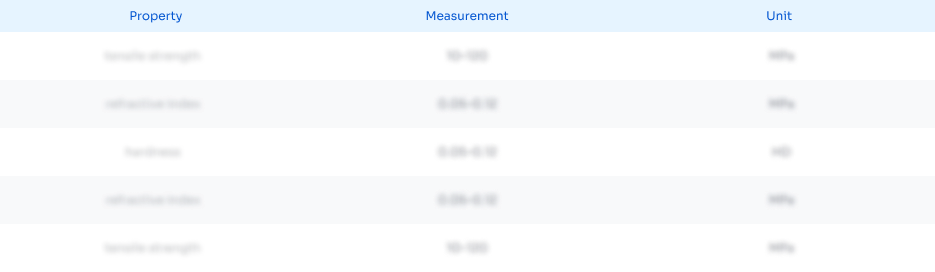
Abstract
Description
Claims
Application Information

- R&D
- Intellectual Property
- Life Sciences
- Materials
- Tech Scout
- Unparalleled Data Quality
- Higher Quality Content
- 60% Fewer Hallucinations
Browse by: Latest US Patents, China's latest patents, Technical Efficacy Thesaurus, Application Domain, Technology Topic, Popular Technical Reports.
© 2025 PatSnap. All rights reserved.Legal|Privacy policy|Modern Slavery Act Transparency Statement|Sitemap|About US| Contact US: help@patsnap.com