Ethylene oxide purification method
A technology of ethylene oxide and separation method, applied in the direction of organic chemistry and the like, can solve the problems of low absorption rate and removal rate of ethylene oxide and high energy consumption, and achieve good absorption effect, low energy consumption and good separation effect. Effect
- Summary
- Abstract
- Description
- Claims
- Application Information
AI Technical Summary
Benefits of technology
Problems solved by technology
Method used
Image
Examples
Embodiment 1
[0026] 50°C low-concentration ethylene oxide (molar concentration: 1mol% EO, 10% CO) from the outlet of the reactor 2 , 22%C 2 h 4 , 5%O 2 , 55% CH 4 , 7% Ar) into the absorption tower, the operating pressure is 20bar, and the absorbent is 50% 1-hexyl-3-methylimidazolium hexafluorophosphate ([hmim][PF 6 ]) and 50% triethylene glycol dimethyl ether (TEGDM), and the feed gas mass ratio is 3; after the absorption process, ethylene oxide in the oxirane removal gas is 30ppm, and the ethylene oxide absorption rate is 99.9% or more. The rich liquid enters the 2bar flash tank, and most of the CO in the absorbent 2 , C 2 h 4 , O 2 , CH 4 and Ar are desorbed; the absorption liquid is heated to 100°C and enters a 0.01bar desorption tower, and the molar concentration of 92% ethylene oxide at the top of the tower enters the subsequent ethylene oxide purification section, and the removal rate of ethylene oxide is at More than 99%, the lean liquid in the tower kettle is cooled to 5...
Embodiment 2
[0028] 60°C low-concentration ethylene oxide (molar concentration: 1mol% EO, 10% CO) from the outlet of the reactor 2 , 22%C 2 h 4 , 5%O 2 , 55% CH 4, 7% Ar) into the absorption tower, the operating pressure is 20bar, and the absorbent is 70[hmim][PF 6 ] and 30% TEGDM, with a mass ratio of 3 to the feed gas; after the absorption process, the ethylene oxide in the ethylene oxide gas is 25ppm, and the ethylene oxide absorption rate is above 99.9%. The rich liquid enters the 2bar flash tank, and most of the CO in the absorbent 2 , C 2 h 4 , O 2 , CH 4 and Ar are desorbed; the absorption liquid is heated to 100°C and enters a 0.01bar desorption tower, and the molar concentration of 92% ethylene oxide at the top of the tower enters the subsequent ethylene oxide purification section, and the removal rate of ethylene oxide is at More than 99%, the lean liquid in the tower kettle is cooled to 60°C by heat exchange and returned to the absorption tower.
Embodiment 3
[0030] 80°C low-concentration ethylene oxide (molar concentration: 1mol% EO, 10% CO) from the outlet of the reactor 2 , 22%C 2 h 4 , 5%O 2 , 55% CH 4 , 7% Ar) into the absorption tower, the operating pressure is 20bar, and the absorbent is 80[hmim][PF 6 ] and 20% TEGDM, with a mass ratio of 5 to the feed gas; after the absorption process, the ethylene oxide in the ethylene oxide gas is 30ppm, and the ethylene oxide absorption rate is above 99.9%. The rich liquid enters the 2bar flash tank, and most of the CO in the absorbent 2 , C 2 h 4 , O 2 , CH 4 and Ar are desorbed; the absorption liquid is heated to 100°C and enters a 0.01bar desorption tower, and the molar concentration of 92% ethylene oxide at the top of the tower enters the subsequent ethylene oxide purification section, and the removal rate of ethylene oxide is at More than 99%, the lean liquid in the tower kettle is cooled to 80°C by heat exchange and returned to the absorption tower.
PUM
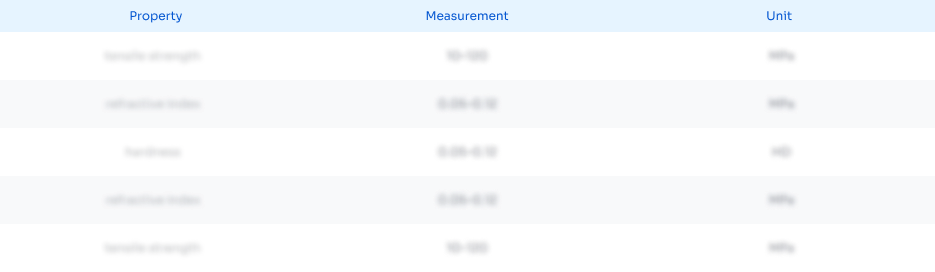
Abstract
Description
Claims
Application Information

- R&D
- Intellectual Property
- Life Sciences
- Materials
- Tech Scout
- Unparalleled Data Quality
- Higher Quality Content
- 60% Fewer Hallucinations
Browse by: Latest US Patents, China's latest patents, Technical Efficacy Thesaurus, Application Domain, Technology Topic, Popular Technical Reports.
© 2025 PatSnap. All rights reserved.Legal|Privacy policy|Modern Slavery Act Transparency Statement|Sitemap|About US| Contact US: help@patsnap.com