Reaction device and reaction method for catalytic gasification combined fluidized bed
A reaction device, catalytic gasification technology, applied in the gasification process, granular/powdered fuel gasification, combustible gas production, etc., can solve the problems of low methane yield, low carbon conversion rate and gasification intensity, and gasifier operation Problems such as poor stability and reliability, to achieve high carbon conversion rate, improved carbon conversion rate, efficient and stable reaction
- Summary
- Abstract
- Description
- Claims
- Application Information
AI Technical Summary
Problems solved by technology
Method used
Image
Examples
Embodiment 1
[0029] The reaction process is as follows: Catalyst and carbon-containing raw materials enter the settler from the feed pipeline, are introduced into the fine reactor by the feeding mechanism, and are mixed with water vapor and oxygen from the gas pipeline to carry out gasification reaction in the fine reactor After the reaction, the large-particle slag falls into the slag pool through natural settlement, and is separated from the slag by the catalyst recovery equipment and recovered from the slag pool to recover the catalyst. The carbon-containing particles reacted in the fine reactor are lifted into the coarse reactor by gas for further gasification reaction. The reacted gas and solid fine ash, carbon-containing particles and slag enter the separation equipment. After separation, the gas, part of the fine ash and carbon-containing particles are discharged by the cyclone and enter the fast reactor for rapid gasification reaction, and then The product gas, fine ash and partial...
Embodiment 2
[0032] The reaction process is the same as in Example 1. In the experiment, Inner Mongolia lignite was selected, and it was crushed to make pulverized coal below 1mm and mixed with 5% potassium carbonate catalyst. The diameter of the fine reactor is 50mm, the height is 3000mm, the linear velocity is 2m / s, the water-carbon ratio is 1mol / mol, the reaction temperature is 800°C, and the reaction pressure is 2MPa; the diameter of the coarse reactor is 300mm, the height is 1500mm, and the reaction temperature is 650°C, reaction pressure 2MPa. The loading amount of the catalyst accounts for 5% of the raw coal mass. The amount of circulating synthesis gas accounts for 20% of the total output of the gasification unit, and the ratio of hydrogen to carbon monoxide in the circulating synthesis gas is 1. Due to the high separation efficiency, there are very few particles leaving the separation equipment, so the fast reactor is a tubular reactor, and the operating temperature is 850°C. T...
Embodiment 3
[0034] The reaction process is the same as in Example 1. In the experiment, Inner Mongolia lignite was selected, and it was crushed to make pulverized coal below 1mm and mixed with 5% potassium carbonate catalyst. The diameter of the fine reactor is 50mm, the height is 3000mm, the linear velocity is 2m / s, the water-carbon ratio is 1mol / mol, the reaction temperature is 800°C, and the reaction pressure is 2MPa; the diameter of the coarse reactor is 150mm, the height is 1500mm, and the reaction temperature is 650°C, reaction pressure 2MPa. The loading amount of the catalyst accounts for 5% of the raw coal mass. The amount of circulating synthesis gas accounts for 20% of the total output of the gasification unit, and the ratio of hydrogen to carbon monoxide in the circulating synthesis gas is 1. Due to the high separation efficiency, there are very few particles leaving the separation equipment, so the fast reactor is a tubular reactor, and the operating temperature is 850°C. T...
PUM
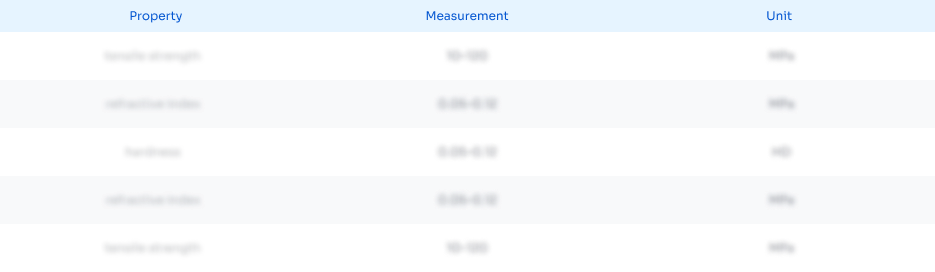
Abstract
Description
Claims
Application Information

- R&D
- Intellectual Property
- Life Sciences
- Materials
- Tech Scout
- Unparalleled Data Quality
- Higher Quality Content
- 60% Fewer Hallucinations
Browse by: Latest US Patents, China's latest patents, Technical Efficacy Thesaurus, Application Domain, Technology Topic, Popular Technical Reports.
© 2025 PatSnap. All rights reserved.Legal|Privacy policy|Modern Slavery Act Transparency Statement|Sitemap|About US| Contact US: help@patsnap.com