Waste heat annealing system suitable for total oxygen kiln furnace
A waste heat annealing and kiln furnace technology, which is applied in furnaces, waste heat treatment, furnace components, etc., can solve the problems of high temperature of exhausted smoke and waste heat that cannot be used beneficially
- Summary
- Abstract
- Description
- Claims
- Application Information
AI Technical Summary
Problems solved by technology
Method used
Image
Examples
Embodiment 1
[0029] Such as figure 1 As shown, the waste heat annealing system suitable for an all-oxygen furnace includes an all-oxygen furnace 1 and an annealing furnace 2. The top of the all-oxygen furnace 1 is provided with a smoke outlet channel 6, wherein a heat exchanger 3 is arranged on the smoke outlet channel 6. The air inlet of the heat exchanger 3 is connected with the air inlet pipe 7, the air outlet of the heat exchanger 3 is connected with one end of the heat preservation pipe 9, the other end of the heat preservation pipe 9 is connected with the air inlet of the annealing furnace 2, and the air outlet of the annealing furnace 2 is connected with the air outlet of the annealing furnace 2. The air duct 8 is connected, the air inlet duct 7 is provided with an induced draft fan 4, and the thermal insulation pipe 9 is provided with a heat-regulating fan 5.
[0030] In use, a heat exchanger is installed on the smoke outlet channel of the all-oxygen kiln furnace. The clean air fro...
Embodiment 2
[0033] Based on Example 1, such as image 3 As shown, the heat exchanger 3 includes a shell, a heat exchange chamber 16 and a heat exchange tube 15, and the two ends of the heat exchange tube 15 communicate with the air inlet tube 7 and the heat preservation tube 9 respectively. The smoke outlet channel 6 passes through the shell of the heat exchanger 3 , and the heat exchange tube 15 is wound on a section of the smoke outlet channel 6 located in the heat exchange chamber 16 .
[0034] In use, the smoke outlet channel is passed through the shell of the heat exchanger, and the heat exchange tube is wound on the smoke outlet channel, which can increase the contact area between the smoke outlet channel and the heat exchange tube, thereby improving the heat exchange effect.
Embodiment 3
[0036] Based on Example 1, such as Figure 4 As shown, the heat exchanger 3 includes a shell, a heat exchange chamber 16 and a heat exchange tube 15, and the two ends of the heat exchange tube 15 communicate with the air inlet tube 7 and the heat preservation tube 9 respectively. The smoke outlet channel 6 is connected to the bottom of the shell of the heat exchanger 3 and communicated with the heat exchange chamber 16. The top of the shell of the heat exchanger 3 is provided with a smoke exhaust pipe 17 communicated with the heat exchange chamber 16. The heat exchange pipe 15 is in the shape of a snake. The two ends of the heat exchange tube 15 are located on both sides of the shell of the heat exchanger 3 respectively.
[0037] This embodiment provides another heat exchanger structure, which connects the smoke outlet channel to the bottom of the heat exchanger shell, so that the high-temperature gas in the smoke outlet channel can fill the heat exchange chamber, which is con...
PUM
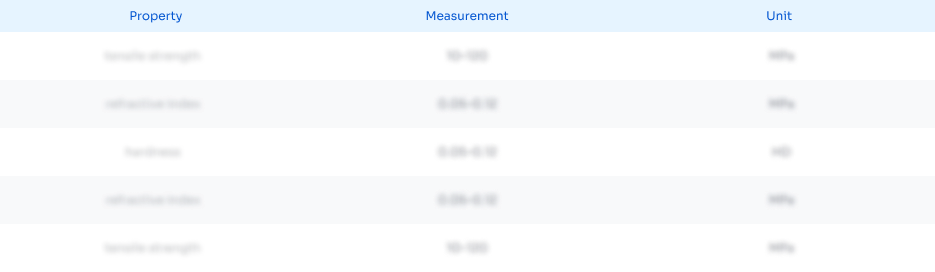
Abstract
Description
Claims
Application Information

- R&D
- Intellectual Property
- Life Sciences
- Materials
- Tech Scout
- Unparalleled Data Quality
- Higher Quality Content
- 60% Fewer Hallucinations
Browse by: Latest US Patents, China's latest patents, Technical Efficacy Thesaurus, Application Domain, Technology Topic, Popular Technical Reports.
© 2025 PatSnap. All rights reserved.Legal|Privacy policy|Modern Slavery Act Transparency Statement|Sitemap|About US| Contact US: help@patsnap.com