Robot shaft hole assembly system and method based on teaching learning
An assembly method and technology of an assembly system, which are used in manipulators, program-controlled manipulators, metal processing equipment, etc., can solve the problems of low manual operation efficiency, high operator requirements, and only used in structured environments, so as to avoid calibration. Work, good algorithm versatility, easy algorithm transplantation effect
- Summary
- Abstract
- Description
- Claims
- Application Information
AI Technical Summary
Problems solved by technology
Method used
Image
Examples
Embodiment Construction
[0042] (2) if figure 2As shown, the control system block diagram includes a mechanical arm 1, a six-dimensional force / torque sensor 2, and a PC host computer 4. The six-dimensional force / torque sensor 2 is used to measure contact force, and the mechanical arm 1 has motion control Functional multi-axis manipulator 1, six-dimensional force / torque sensor 2 is installed at the end of manipulator 1, passive flexible RCC device 3 is installed on six-dimensional force / torque sensor 2, PC host computer 4 is connected with manipulator 1 and six-dimensional force The / torque sensor 2 is connected by communication. During operation, the mechanical arm 1 carries the passive flexible RCC device 3 under the control instruction of the PC host computer 4 to carry out the shaft hole assembly of the clamping pin parts. The control system built by the PC host computer 4 is based on ROS platform. The control system is based on the ROS platform and includes a control algorithm node, a feedback n...
PUM
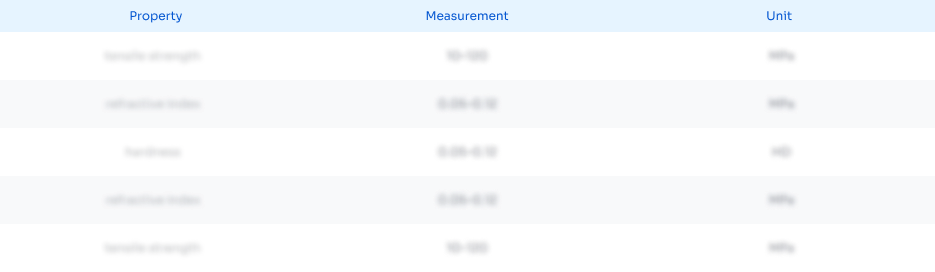
Abstract
Description
Claims
Application Information

- R&D
- Intellectual Property
- Life Sciences
- Materials
- Tech Scout
- Unparalleled Data Quality
- Higher Quality Content
- 60% Fewer Hallucinations
Browse by: Latest US Patents, China's latest patents, Technical Efficacy Thesaurus, Application Domain, Technology Topic, Popular Technical Reports.
© 2025 PatSnap. All rights reserved.Legal|Privacy policy|Modern Slavery Act Transparency Statement|Sitemap|About US| Contact US: help@patsnap.com