Chemical fiber cloth production method
A production method and technology of chemical fiber cloth, applied in the field of textile fabrics, can solve the problems of affecting the production environment, poor water absorption performance of chemical fiber cloth, difficult to absorb sweat, etc., and achieve the effects of improving quality, absorbing sweat well, and improving water absorption performance.
- Summary
- Abstract
- Description
- Claims
- Application Information
AI Technical Summary
Problems solved by technology
Method used
Image
Examples
Embodiment 1
[0020] A method for making a chemical fiber cloth, comprising the steps of:
[0021] Step 1: Yarn selection and weaving: select acrylic fiber as the warp thread, choose cotton yarn as the weft thread, and weave the warp thread and weft thread into fabric through the weaving machine.
[0022] Step 2: Bleaching and dipping: put the fabric in step 1 into the dipping device for dipping, add liquid alkali and brightener to the dipping device, the liquid alkali is 1% of the fabric weight; the brightener is 2% of the fabric weight, And add an anti-corrosion agent, the anti-corrosion agent is 10% of the weight of the fabric, and the soaking time is 3 to 4 hours.
[0023] Step 3: Dyeing liquid ingredients:
[0024] The dyeing solution includes 3 parts of polyethylene resin, 3 parts of oxidized butyl benzoate, 0.5 parts of maleic anhydride grafted polyethylene, 4 parts of hydroxypropyl methylcellulose, 1 part of vegetable dye, and 1 part of seafoam according to the proportion by weight...
Embodiment 2
[0029] A method for making a chemical fiber cloth, comprising the steps of:
[0030] Step 1: Yarn selection and weaving: select acrylic fiber as the warp thread, choose cotton yarn as the weft thread, and weave the warp thread and weft thread into fabric through the weaving machine.
[0031] Step 2: Bleaching and dipping: put the fabric in step 1 into the dipping device for dipping, add liquid alkali and brightener to the dipping device, the liquid alkali is 1% of the fabric weight; the brightener is 2% of the fabric weight, And add an anti-corrosion agent, the anti-corrosion agent is 10% of the weight of the fabric, and the soaking time is 3 to 4 hours.
[0032] Step 3: Dyeing liquid ingredients:
[0033] The dyeing solution includes 7 parts of polyethylene resin, 5 parts of oxidized butyl benzoate, 0.8 parts of maleic anhydride grafted polyethylene, 8 parts of hydroxypropyl methylcellulose, 2 parts of vegetable dyes, and 2 parts of sea foam according to the weight ratio. 1...
Embodiment 3
[0038] A method for making a chemical fiber cloth, comprising the steps of:
[0039] Step 1: Yarn selection and weaving: select acrylic fiber as the warp thread, choose cotton yarn as the weft thread, and weave the warp thread and weft thread into fabric through the weaving machine.
[0040] Step 2: Bleaching and dipping: put the fabric in step 1 into the dipping device for dipping, add liquid alkali and brightener to the dipping device, the liquid alkali is 1% of the fabric weight; the brightener is 2% of the fabric weight, And add an anti-corrosion agent, the anti-corrosion agent is 10% of the weight of the fabric, and the soaking time is 3 to 4 hours.
[0041] Step 3: Dyeing liquid ingredients:
[0042] The dyeing solution includes 5 parts of polyethylene resin, 4 parts of oxidized butyl benzoate, 0.7 parts of maleic anhydride grafted polyethylene, 6 parts of hydroxypropyl methylcellulose, 1.5 parts of vegetable dyes, sea foam 8 parts of stone fiber, 11 parts of aminoprop...
PUM
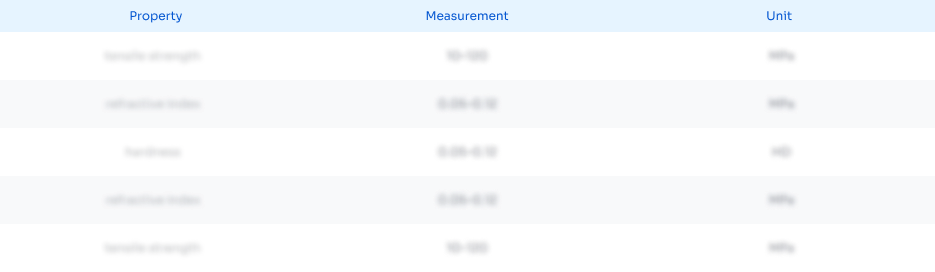
Abstract
Description
Claims
Application Information

- Generate Ideas
- Intellectual Property
- Life Sciences
- Materials
- Tech Scout
- Unparalleled Data Quality
- Higher Quality Content
- 60% Fewer Hallucinations
Browse by: Latest US Patents, China's latest patents, Technical Efficacy Thesaurus, Application Domain, Technology Topic, Popular Technical Reports.
© 2025 PatSnap. All rights reserved.Legal|Privacy policy|Modern Slavery Act Transparency Statement|Sitemap|About US| Contact US: help@patsnap.com