Refining desizing process for chemical fiber fabric
A fabric and chemical fiber technology, applied in the field of textile printing and dyeing pretreatment, can solve the problems of difficult degree of control, low dyeing percentage of fabrics, poor dyeing uniformity, etc., and achieves the effect of eliminating burrs, improving dyeing uniformity and eliminating rust.
- Summary
- Abstract
- Description
- Claims
- Application Information
AI Technical Summary
Problems solved by technology
Method used
Image
Examples
Embodiment 1
[0036] Embodiment 1: a kind of scouring desizing process of chemical fiber fabric, comprises the following steps:
[0037] (1) Pre-shrinking: pre-shrinking chemical fiber fabrics in the open-width two-dipping and two-rolling pre-shrinking machine, the temperature of the first water tank is controlled at 85°C, the temperature of the second water tank is 90°C, and the chemical fiber fabrics pass through each water tank The moving speed is 30 m / min, and the washing time of each tank is 30 minutes;
[0038] (2) Scouring: use oxalic acid with a mass concentration of 1% to soak the chemical fiber fabric for 30 minutes, and the water-to-bath ratio is 1:10. The final chemical fiber fabric is placed in the overflow dyeing machine, the mass ratio of the chemical fiber fabric and the scouring liquid is controlled to be 1:20, and then lye solution with a mass fraction of 30% is added, the scouring temperature is controlled to be 100° C., and the scouring time is 30 minutes. The moving sp...
Embodiment 2-7
[0050] Example 2-7: A scouring and desizing process for chemical fiber fabrics. The difference from Example 1 is that the components in the scouring liquid and the parts by weight corresponding to each component are shown in Table 1.
[0051] Components of scouring liquor and the corresponding parts by weight of each component in Table 1 embodiment 2-7
[0052]
[0053]
Embodiment 8
[0054] Embodiment 8: A scouring and desizing process for chemical fiber fabrics. The difference from Embodiment 1 is that the penetrating agent includes triisobutyl phosphate and sodium secondary alkyl sulfonate at a ratio of 3:1.
PUM
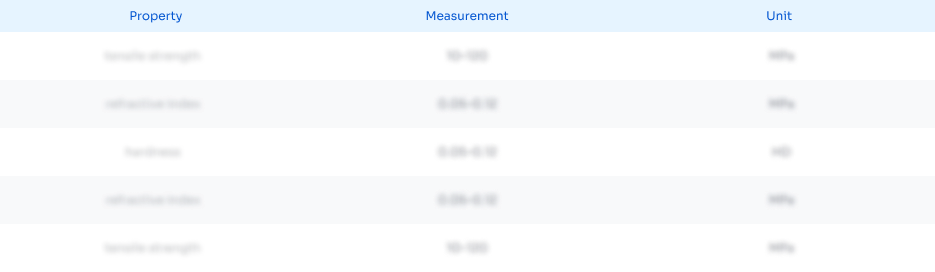
Abstract
Description
Claims
Application Information

- R&D
- Intellectual Property
- Life Sciences
- Materials
- Tech Scout
- Unparalleled Data Quality
- Higher Quality Content
- 60% Fewer Hallucinations
Browse by: Latest US Patents, China's latest patents, Technical Efficacy Thesaurus, Application Domain, Technology Topic, Popular Technical Reports.
© 2025 PatSnap. All rights reserved.Legal|Privacy policy|Modern Slavery Act Transparency Statement|Sitemap|About US| Contact US: help@patsnap.com