Microstructure mixer for high-viscosity fluid mixing
A microstructure mixer and fluid mixing technology, which is applied in the direction of fluid mixers, mixers, chemical instruments and methods, etc., can solve problems such as limiting mixing effects, and achieve the effect of reducing flow resistance and quickly and uniformly mixing
- Summary
- Abstract
- Description
- Claims
- Application Information
AI Technical Summary
Problems solved by technology
Method used
Image
Examples
Embodiment 1
[0020] Use the glycerin aqueous solution (viscosity=100mPas) that contains rhodamine B as mixing medium, contain 1 width 5mm in the micro mixer, the mixing channel of height 1mm, the mixing channel both sides contain 1 group of width 0.4mm, the microgroove of length 10mm, The glycerin solution flow rate that enters from feed inlet (6) is 20mL / min, the glycerol solution flow rate that enters from main feed inlet (7) is 10mL / min, and measurement obtains mixing factor=0.95, and the maximum flow resistance of mixer is 0.1MPa.
Embodiment 2
[0022] Use the glycerol aqueous solution (viscosity=100mPas) that contains rhodamine B as mixing medium, contain 10 width 1mm in the micro mixer, the mixing channel of height 1mm, the mixing channel both sides contain 1 group of width 0.2mm, the microgroove of length 4mm, The glycerin solution flow rate that enters from feed inlet (6) is 100mL / min, the glycerol solution flow rate that enters from main feed inlet (7) is 50mL / min, and measurement obtains mixing factor=0.93, and the maximum flow resistance of mixer is 0.3MPa.
Embodiment 3
[0024] Use the polyvinyl alcohol aqueous solution (viscosity=500mPas) that contains Rhodamine B as the mixing medium, contain 1 width 20mm, the mixing channel of height 4mm in the micro-mixer, there are 2 groups of microgrooves with width 1mm and length 30mm on both sides of the mixing channel , the flow rate of the polyvinyl alcohol solution entering from the feed port (6) is 50mL / min, the flow rate of the polyvinyl alcohol solution entering from the main feed port (7) is 5mL / min, the measurement results in a mixing factor=0.90, and the mixer has the highest Flow resistance 0.1MPa.
PUM
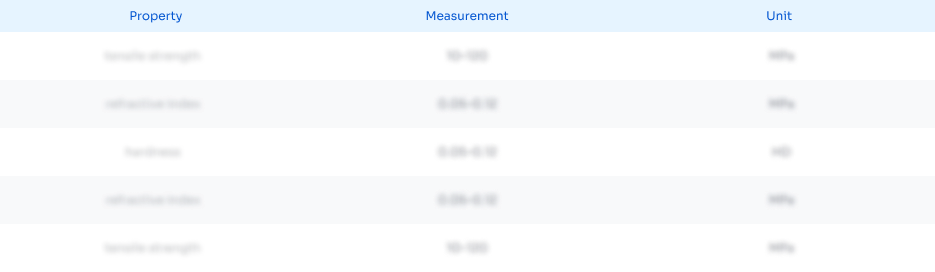
Abstract
Description
Claims
Application Information

- R&D
- Intellectual Property
- Life Sciences
- Materials
- Tech Scout
- Unparalleled Data Quality
- Higher Quality Content
- 60% Fewer Hallucinations
Browse by: Latest US Patents, China's latest patents, Technical Efficacy Thesaurus, Application Domain, Technology Topic, Popular Technical Reports.
© 2025 PatSnap. All rights reserved.Legal|Privacy policy|Modern Slavery Act Transparency Statement|Sitemap|About US| Contact US: help@patsnap.com