A degassing assembly line for electric cables
An air flow and cable technology, applied in the field of degassing water lines for cables, can solve the problems of moving to the inner layer of insulation, unsatisfactory effect, reverse movement of space charges, etc., saving degassing time, good degassing effect, and improving production. The effect of efficiency
- Summary
- Abstract
- Description
- Claims
- Application Information
AI Technical Summary
Problems solved by technology
Method used
Image
Examples
Embodiment Construction
[0022] The preferred embodiments of the present invention will be described in detail below in conjunction with the accompanying drawings, so that the advantages and features of the present invention can be more easily understood by those skilled in the art, so as to define the protection scope of the present invention more clearly.
[0023] see Figure 1 to Figure 3 , the embodiment of the present invention includes: a degassing water line for cables, including: a vertical tower extruder 16 and a degassing room 17, the vertical tower extruder 16 and the degassing room 17 are insulated by cables The wire cores 18 are connected, and the tower extruder 16 is used to produce the cable insulation wire cores 18 .
[0024] The cable insulation core 18 is composed of a copper core stranded conductor 13 and a shielding insulation layer 14 , and the shielding insulation layer 14 is wrapped on the outer wall of the copper core stranded conductor 13 .
[0025] Between the vertical tower...
PUM
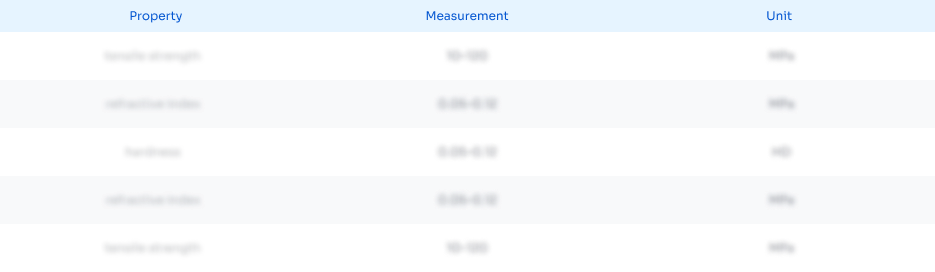
Abstract
Description
Claims
Application Information

- R&D
- Intellectual Property
- Life Sciences
- Materials
- Tech Scout
- Unparalleled Data Quality
- Higher Quality Content
- 60% Fewer Hallucinations
Browse by: Latest US Patents, China's latest patents, Technical Efficacy Thesaurus, Application Domain, Technology Topic, Popular Technical Reports.
© 2025 PatSnap. All rights reserved.Legal|Privacy policy|Modern Slavery Act Transparency Statement|Sitemap|About US| Contact US: help@patsnap.com