High speed optimized truncating and finish planing production line
A production line and fine planing technology, used in circular saws, workpiece feeding devices, processing machines for manufacturing flat surfaces, etc. The effect of increased production efficiency, fast cut-off and advance feed
- Summary
- Abstract
- Description
- Claims
- Application Information
AI Technical Summary
Problems solved by technology
Method used
Image
Examples
Embodiment Construction
[0044] Such as figure 1 The high-speed preferred cut-off fine-planing production line includes the preferred cut-off saw 4 and the planer 1, the preferred cut-off saw 4 adopts the preferred cut-off saw in the woodworking direction, and the planer milling machine 1 is a woodworking four-sided planer; the preferred cut-off saw 4 It is connected with the planer 1 through the cutting material conveying device 2 , preferably the feeding end of the cutting saw 4 is connected with the feeding conveying device 5 , and the cutting material conveying device 2 is also provided with a sorting pusher 3 .
[0045] Such as figure 2 , image 3 Shown feeding conveying device 5, the feeding frame 5-11 of this feeding conveying device 5 is connected with the preferred cut-off saw frame, and worktable 5-14 is fixedly installed on the feeding frame 5-11, On the preferred cut-off saw frame, the cut-off saw table is fixedly installed, the cut-off saw work table and the work table 5-14 are connect...
PUM
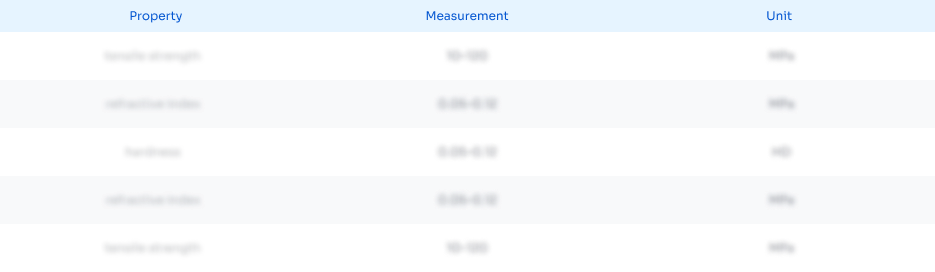
Abstract
Description
Claims
Application Information

- R&D
- Intellectual Property
- Life Sciences
- Materials
- Tech Scout
- Unparalleled Data Quality
- Higher Quality Content
- 60% Fewer Hallucinations
Browse by: Latest US Patents, China's latest patents, Technical Efficacy Thesaurus, Application Domain, Technology Topic, Popular Technical Reports.
© 2025 PatSnap. All rights reserved.Legal|Privacy policy|Modern Slavery Act Transparency Statement|Sitemap|About US| Contact US: help@patsnap.com