Human-machine cooperative picking robot based on Leap Motion and machine vision and control method thereof
A picking robot and human-machine collaboration technology, applied in the direction of program-controlled manipulators, agricultural machinery and implements, manipulators, etc., can solve the problems of single results, or clustered results, difficult to distinguish fruits, etc., to reduce intervention, reduce processing, The effect of improving the degree of intelligence
- Summary
- Abstract
- Description
- Claims
- Application Information
AI Technical Summary
Problems solved by technology
Method used
Image
Examples
Embodiment Construction
[0036] The present invention will be described in detail below in conjunction with accompanying drawing:
[0037] like Figure 1-7 Shown:
[0038] The human-machine collaborative picking robot based on Leap Motion and machine vision includes a crawler-type work platform vehicle 4, a remote control system and a picking robot arm 6, and a generator (not shown) is installed on the crawler-type work platform vehicle 4 through fastening bolts , picking the collection basket 5 and the robot controller 3, and the generator is electrically connected with the robot controller 3.
[0039] The remote control system includes a computer 1 and a Leap Motion somatosensory sensor 2, the Leap Motion somatosensory sensor 2 is connected to the computer 1 through a data cable, and the computer 1 is connected to the robot controller 3 through a GPRS communication.
[0040] The picking mechanical arm 6 comprises a base upper plate 12, a base lower plate 14, a boom 9 and a forearm 7, the base lowe...
PUM
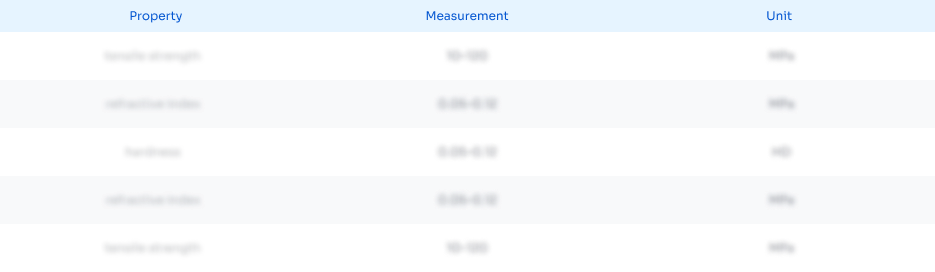
Abstract
Description
Claims
Application Information

- R&D Engineer
- R&D Manager
- IP Professional
- Industry Leading Data Capabilities
- Powerful AI technology
- Patent DNA Extraction
Browse by: Latest US Patents, China's latest patents, Technical Efficacy Thesaurus, Application Domain, Technology Topic, Popular Technical Reports.
© 2024 PatSnap. All rights reserved.Legal|Privacy policy|Modern Slavery Act Transparency Statement|Sitemap|About US| Contact US: help@patsnap.com