A rotor structure optimization method based on central composite design
A composite design and rotor structure technology, applied in design optimization/simulation, multi-objective optimization, manufacturing stator/rotor body, etc., can solve the problem of finite element grids that consume a lot of time and computer resources, and thermal structure coupling analysis models. and other problems to achieve the effect of saving computer resources and improving the optimization effect
- Summary
- Abstract
- Description
- Claims
- Application Information
AI Technical Summary
Problems solved by technology
Method used
Image
Examples
Embodiment Construction
[0030] Embodiments of the present invention will be described in detail below in conjunction with the accompanying drawings.
[0031] see figure 1 As shown, the present invention provides a rotor structure optimization method based on central composite design, including the following steps:
[0032] 1. Determine the design variables for rotor structure optimization and determine the value range of the design variables.
[0033] For a certain type of rotor, selecting the structure to be optimized often requires n parameters to determine its specific geometric shape; at the same time, in order to avoid mutual interference within the structure and prevent errors in operations such as establishing geometric surfaces, it is necessary to determine Range and constraints of design variables.
[0034] by figure 2 The rotor in is taken as an example, from the overall structure diagram of the rotor and the local structure diagram to be optimized, the groove structure is determined by...
PUM
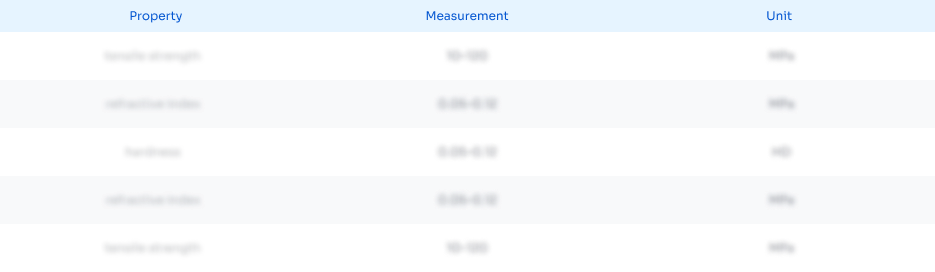
Abstract
Description
Claims
Application Information

- R&D
- Intellectual Property
- Life Sciences
- Materials
- Tech Scout
- Unparalleled Data Quality
- Higher Quality Content
- 60% Fewer Hallucinations
Browse by: Latest US Patents, China's latest patents, Technical Efficacy Thesaurus, Application Domain, Technology Topic, Popular Technical Reports.
© 2025 PatSnap. All rights reserved.Legal|Privacy policy|Modern Slavery Act Transparency Statement|Sitemap|About US| Contact US: help@patsnap.com