Tool wear image stitching method and tool life prediction method
A tool wear and image technology, which is applied to the details of image stitching, image enhancement, image analysis, etc., can solve the problems of workpiece scrapping and life prediction.
- Summary
- Abstract
- Description
- Claims
- Application Information
AI Technical Summary
Problems solved by technology
Method used
Image
Examples
specific Embodiment approach 1
[0062] This embodiment is a method for mosaicing tool wear images, including the following steps:
[0063] Step 1. Collect images:
[0064] Take each edge face and bottom face (cutter face) of the tool as the object, and collect the wear image A of the bottom face of the tool 0 , and the wear image of the blade surface is collected continuously along each blade surface Ensure that two adjacent images have overlapping areas; q is the serial number of each blade surface, q=1,2,...,Q; Q is the total number of blade surfaces; the subscript "w" is the number of images collected along the blade surface sequence number;
[0065] The blade surface of the tool is helical. When collecting each blade surface, the image acquisition device needs to spirally rise along the blade surface to continuously collect images of the blade surface, and ensure that images with overlapping areas are continuously collected along the blade surface; The sequence number of is marked as w;
[0066] Tak...
specific Embodiment approach 2
[0073] The specific process of step 3 is as follows:
[0074] According to the H, S, V values of the HSV color space, a Cartesian coordinate system is established, and the space vector modulus is taken As the feature value, select two adjacent images that need to be spliced, calculate the space vector modulo P for each pixel, and use the area with the same P value in the two images as the area to be fused (corresponding to the overlapped area in the two images part), the four vertices of the area to be fused are recorded as A, B, C, D and A', B', C', D' in the two images, and the eight vertices are determined in the Cartesian coordinate system Coordinates, and determine the vector representations of AB and A'B' respectively, which are recorded as AB(m, n) and A'B'(e, f), and use point A as the reference point to establish the translation between A and A' Transformation equation g(x, y) = g 1 (x+x A -x A’ ,y+y A -y A’ );
[0075] Among them, x and y respectively rep...
specific Embodiment approach 3
[0079] The specific process of converting the R, G, and B values of the RGB color space into the H, S, and V values of the HSV color space described in step 2 is as follows:
[0080]
[0081]
[0082]
[0083]
[0084] Among them, H, S, and V are the H, S, and V values of the HSV color space, respectively.
PUM
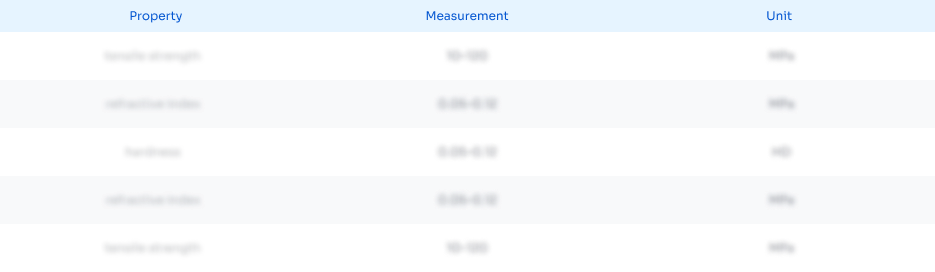
Abstract
Description
Claims
Application Information

- Generate Ideas
- Intellectual Property
- Life Sciences
- Materials
- Tech Scout
- Unparalleled Data Quality
- Higher Quality Content
- 60% Fewer Hallucinations
Browse by: Latest US Patents, China's latest patents, Technical Efficacy Thesaurus, Application Domain, Technology Topic, Popular Technical Reports.
© 2025 PatSnap. All rights reserved.Legal|Privacy policy|Modern Slavery Act Transparency Statement|Sitemap|About US| Contact US: help@patsnap.com