Electron beam welding method for large-thickness inclined-angle welding joint
A technology of electron beam welding and tilting angle, which is applied in the direction of electron beam welding equipment, welding equipment, metal processing equipment, etc., can solve the problems of non-fusion, inconvenient operation, welding deviation at the root of large-thick weld seam, etc., and achieve the goal of avoiding tilting angle Influence, prevent unfused defects, avoid too narrow effect
- Summary
- Abstract
- Description
- Claims
- Application Information
AI Technical Summary
Problems solved by technology
Method used
Image
Examples
Embodiment Construction
[0039] The present invention will be further described below in conjunction with the accompanying drawings.
[0040] Figure 4 It is the process flow diagram of the present invention, adopting the inclined electron gun welding method to carry out the electron beam welding of the large-thickness inclined-angle weld seam, and avoid the method of welding defects such as welding deviation and lack of fusion, including the following steps:
[0041]Step 1. Process the inner sample block 7 and the outer sample block 8 according to the inclined weld angle α and the welding thickness h marked on the drawings. The outer sample block 8 is a ring structure, and the inner wall is a conical surface; the inner sample block 7 is a multi-section structure, the first section is a conical frustum structure, and a raised structure is set in the center of the large end of the conical frustum, and the second and third sections are cylinders respectively. structure, the diameter of the second secti...
PUM
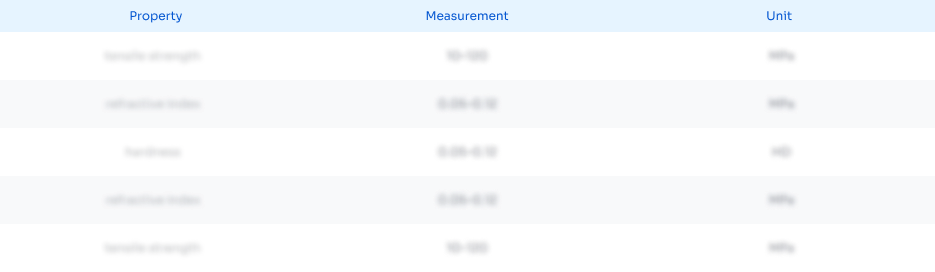
Abstract
Description
Claims
Application Information

- R&D
- Intellectual Property
- Life Sciences
- Materials
- Tech Scout
- Unparalleled Data Quality
- Higher Quality Content
- 60% Fewer Hallucinations
Browse by: Latest US Patents, China's latest patents, Technical Efficacy Thesaurus, Application Domain, Technology Topic, Popular Technical Reports.
© 2025 PatSnap. All rights reserved.Legal|Privacy policy|Modern Slavery Act Transparency Statement|Sitemap|About US| Contact US: help@patsnap.com