Force feedback type anti-falling system
A technology of force feedback and anti-falling, which is applied in the direction of load hanging components, elevators, safety devices, etc., can solve the problems of low anti-falling success rate and slow anti-falling response, and achieve the effect of fast response and direct transmission
- Summary
- Abstract
- Description
- Claims
- Application Information
AI Technical Summary
Problems solved by technology
Method used
Image
Examples
Embodiment 1
[0062] The anti-fall system provided by Embodiment 1 also includes a reset mechanism 5 connected between the actuator 2 and the load mechanism 3; the restoring force of the reset mechanism 5 corresponds to the pulling force of the lifting mechanism 1, when the pulling force of the lifting mechanism 1 is greater than or equal to the reset When the restoring force of the mechanism 4, the lifting mechanism 1 drives the actuator 2 to move relative to the body 31 in the load mechanism 3 and away from the longitudinal track 5; when the pulling force of the lifting mechanism 1 is smaller than the restoring force of the reset mechanism 4, the reset mechanism 4 drives the actuator 2 moves relative to the body 31 in the loading mechanism 3 and approaches the longitudinal rail 5.
[0063] In the first embodiment provided in Example 1, the actuator 2 includes a hinge 21 hinged to the body 31 of the load mechanism 3; the lifting mechanism 1 is directly or indirectly connected to the hinge 2...
Embodiment 2
[0078] The anti-falling system provided by Embodiment 2 also includes a load cell 6 connected between the lifting mechanism 1 and the load mechanism 3; 3 The variation of the applied tension brakes or relaxes the load mechanism 3 . In this way, the actuator 2 is indirectly connected between the lifting mechanism 1 and the loading mechanism 3 , and is used to brake or release the loading mechanism 3 indirectly according to the change of the tension applied by the lifting mechanism 1 to the loading mechanism 3 .
[0079]In this embodiment, the actuator 2 includes an electromagnet 27 and an actuator 28 connected to the electromagnet 27; the electromagnet 27 is electrically connected to the load cell 6, and the actuator 28 is flexibly connected to the body 31 of the load mechanism 3; When the pulling force obtained by the load cell 6 is greater than or equal to the preset value, the electromagnet 27 loses power and moves along the horizontal direction of the body 31 to drive the a...
PUM
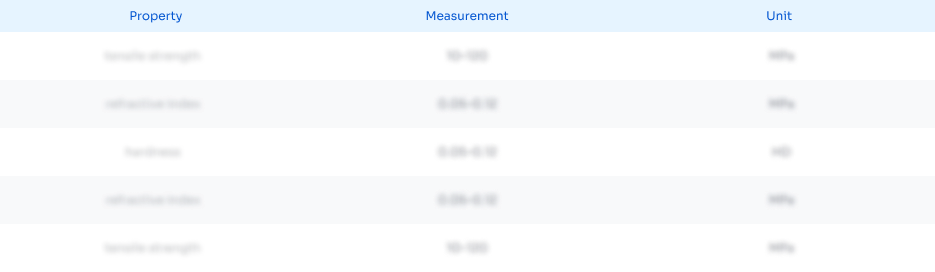
Abstract
Description
Claims
Application Information

- R&D
- Intellectual Property
- Life Sciences
- Materials
- Tech Scout
- Unparalleled Data Quality
- Higher Quality Content
- 60% Fewer Hallucinations
Browse by: Latest US Patents, China's latest patents, Technical Efficacy Thesaurus, Application Domain, Technology Topic, Popular Technical Reports.
© 2025 PatSnap. All rights reserved.Legal|Privacy policy|Modern Slavery Act Transparency Statement|Sitemap|About US| Contact US: help@patsnap.com