Method for reducing iron consumption
A technology for reducing iron and molten iron, applied in the direction of manufacturing converters, improving process efficiency, etc., can solve the problems of low cost, insufficient supply of molten iron, high cost of molten iron, etc., and achieve the effects of simple reduction, stable operation, and simple method of iron consumption
- Summary
- Abstract
- Description
- Claims
- Application Information
AI Technical Summary
Problems solved by technology
Method used
Examples
Embodiment 1
[0028] (1) pour the amount of slag of 40wt% in furnace;
[0029] (2) Pass 97,000t of qualified molten iron into the heating furnace for heating. The heating temperature of the molten iron is 1270°C, and the heating time is 0.8h, and a carbonaceous heating agent is added to the furnace to increase the heat source;
[0030] (3) drop the molten iron heated in the step (2) into the oxygen top-blown converter, and at the same time, add 11000t qualified scrap steel in the oxygen top-blown converter;
[0031] (4) Add slagging material and carry out blowing by lowering the lance. According to the difference in silicon content in the molten iron, the lance position in the blowing process needs to be adjusted specifically. The adjustment steps are as follows:
[0032] A. When the silicon content is 0.10%, the opening gun position is 0.8 meters, the process gun position is 1.1 meters, and the end gun position is 0.8 meters;
[0033] B. When the silicon content is 0.40%, the opening gun ...
Embodiment 2
[0039] (1) pour the amount of slag of 40wt% in furnace;
[0040] (2) Pass 83000t qualified molten iron into the heating furnace for heating, the heating temperature of the molten iron is 1340°C, and the heating time is 1.2h, and a carbonaceous heating agent is added into the furnace to increase the heat source;
[0041] (3) drop the molten iron after heating in the step (2) in the oxygen top-blown converter, at the same time, add 15300t qualified steel scrap in the oxygen top-blown converter;
[0042] (4) Add slagging material and carry out blowing by lowering the lance. According to the difference in silicon content in the molten iron, the lance position in the blowing process needs to be adjusted specifically. The adjustment steps are as follows:
[0043] A. When the silicon content is 0.10%, the opening gun position is 0.8 meters, the process gun position is 1.1 meters, and the end gun position is 0.8 meters;
[0044] B. When the silicon content is 0.40%, the opening gun p...
Embodiment 3
[0050] (1) pour the amount of slag of 40wt% in furnace;
[0051] (2) Pass 85,000t of qualified molten iron into the heating furnace for heating. The heating temperature of the molten iron is 1300°C, and the heating time is 1h, and a carbonaceous heating agent is added to the furnace to increase the heat source;
[0052] (3) drop the molten iron after heating in the step (2) in the oxygen top-blown converter, at the same time, add 15300t qualified steel scrap in the oxygen top-blown converter;
[0053] (4) Add slagging material and carry out blowing by lowering the lance. According to the difference in silicon content in the molten iron, the lance position in the blowing process needs to be adjusted specifically. The adjustment steps are as follows:
[0054] A. When the silicon content is 0.10%, the opening gun position is 0.8 meters, the process gun position is 1.1 meters, and the end gun position is 0.8 meters;
[0055] B. When the silicon content is 0.40%, the opening gun p...
PUM
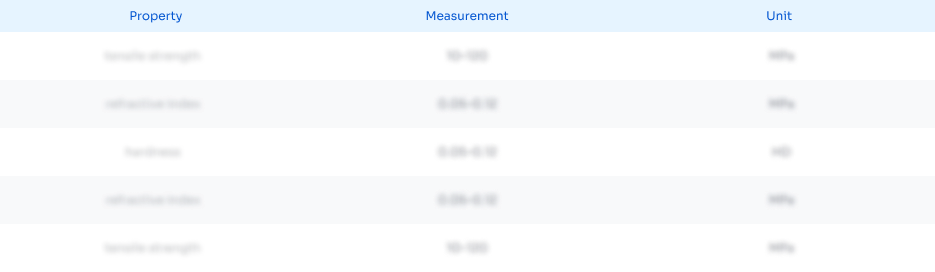
Abstract
Description
Claims
Application Information

- R&D
- Intellectual Property
- Life Sciences
- Materials
- Tech Scout
- Unparalleled Data Quality
- Higher Quality Content
- 60% Fewer Hallucinations
Browse by: Latest US Patents, China's latest patents, Technical Efficacy Thesaurus, Application Domain, Technology Topic, Popular Technical Reports.
© 2025 PatSnap. All rights reserved.Legal|Privacy policy|Modern Slavery Act Transparency Statement|Sitemap|About US| Contact US: help@patsnap.com