Kinematic inverse solution method and device of mechanical arm and mechanical arm
A technology of kinematics inverse solution and mechanical arm, applied in the field of robotics, can solve problems such as complex solution process
- Summary
- Abstract
- Description
- Claims
- Application Information
AI Technical Summary
Problems solved by technology
Method used
Image
Examples
Embodiment 1
[0059] In the preferred embodiment 1 of the present invention, a method for the inverse solution of the kinematics of the manipulator is provided, which can be directly applied to various industrial robots, and can also be applied to other devices with some functions of industrial robots. , can be realized by installing software, APP on industrial robots or other devices, or writing industrial robots or other device controller programs. Specifically, figure 1 An alternative flowchart showing the method, such as figure 1 As shown, the method includes the following steps S102-S106:
[0060] S102: Determine the geometric parameters of the robotic arm, wherein the robotic arm includes a plurality of rotary joints, and the rotary joints are divided into a first-type rotary joint and a second-type rotary joint;
[0061] S104: According to the geometric parameters of the manipulator, determine the first-type joint angle corresponding to the first-type rotary joint by using the geom...
Embodiment 2
[0113] Based on the inverse solution method of the kinematics of the manipulator provided in the above-mentioned embodiment 1, a device for inverse solution of the kinematics of the manipulator is also provided in the preferred embodiment 2 of the present invention, specifically, Figure 6 shows an optional structural block diagram of the device, such as Figure 6 As shown, the device includes:
[0114] The detector 602 is used to determine the geometric parameters of the mechanical arm, wherein the mechanical arm includes a plurality of rotary joints, and the rotary joints are divided into a first type of rotary joint and a second type of rotary joint;
[0115] The first processor 604 is connected to the detector 602, and is configured to determine the first type of joint angle corresponding to the first type of rotary joint by using a geometric algebra method according to the geometric parameters of the mechanical arm;
[0116] The second processor 606, connected to the fir...
Embodiment 3
[0120] Based on the kinematics inversion device of the robotic arm provided in the above-mentioned embodiment 2, a mechanical arm is also provided in preferred embodiment 3 of the present invention, including the above-mentioned kinematics inversion device of the robotic arm.
[0121] In the above-mentioned embodiment, the robot arm is divided into two parts: the front three-arm and the rear three-arm, and use the geometric algebra method and the Euler angle rotation transformation of the wrist to solve the joint angles respectively, without relying on the traditional D-H parameter modeling , which effectively solves the problems in the prior art that the solution process is complex and difficult to understand, the amount of calculation is large, and the solution efficiency is slow, and the solution process is simple and easy to understand, the amount of code is simplified, and the calculation rate is fast and the accuracy is high.
PUM
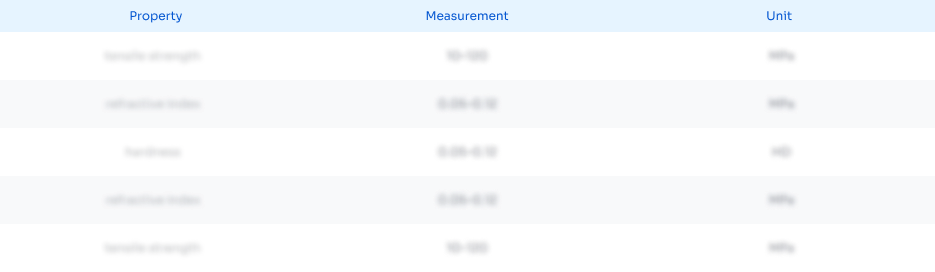
Abstract
Description
Claims
Application Information

- R&D
- Intellectual Property
- Life Sciences
- Materials
- Tech Scout
- Unparalleled Data Quality
- Higher Quality Content
- 60% Fewer Hallucinations
Browse by: Latest US Patents, China's latest patents, Technical Efficacy Thesaurus, Application Domain, Technology Topic, Popular Technical Reports.
© 2025 PatSnap. All rights reserved.Legal|Privacy policy|Modern Slavery Act Transparency Statement|Sitemap|About US| Contact US: help@patsnap.com