Correction method and device for sensor characteristic curve, equipment and storage medium
A sensor characteristic and sensor technology, applied in the sensor field, can solve the problems of affecting sensor calibration and low accuracy.
- Summary
- Abstract
- Description
- Claims
- Application Information
AI Technical Summary
Problems solved by technology
Method used
Image
Examples
Embodiment 1
[0029] figure 1 It is a flow chart of the correction method of the sensor characteristic curve provided by Embodiment 1 of the present invention. This embodiment can be applied to the situation of determining the start and end points (including the starting point and the cut-off point) of the linear interval of the sensor characteristic curve and correcting the sensor characteristic curve. The method can be carried out by means for correcting the sensor characteristic curve, for example a device with processing and calculation functions. Such as figure 1 As shown, the method specifically includes the following steps:
[0030] Step 110, acquiring sample point data of the sensor.
[0031] Among them, the input value of the sensor and its corresponding output value can be obtained by testing the sensor, and the input value (corresponding to the X coordinate) and its corresponding output value (corresponding to the Y coordinate) constitute a point in the coordinate system, and t...
Embodiment approach
[0041] On the basis of the first embodiment above, this embodiment provides a preferred implementation manner of determining the start and end points of the linear interval in step 130, including the following steps:
[0042] (1) Calculate the deviation between the current sample point and the fitted straight line.
[0043] Preferably, the following formula can be used to calculate the deviation D between the sample point and the fitted straight line: D=|kx i +b-y i |, where, the fitting straight line equation is y=kx+b, k and b are both constants of the straight line, k≠0; the coordinates of the sample point i are (x i ,y i ).
[0044] (2) Judging whether the above deviation is smaller than a preset threshold.
[0045] (3) If the above deviation is smaller than the preset threshold, acquire a first preset number of sample points on the preset side of the current sample point in a preset order.
[0046]Wherein, the preset side can be the left side or the right side, which...
Embodiment 3
[0053] On the basis of the first and second embodiments above, this embodiment provides a preferred implementation manner of determining the fitted straight line according to the sample point data in step 120, and the fitting accuracy is relatively high. Specifically include the following steps:
[0054] (1) Extract sample points whose ordinate value is less than the median value in the sample point data.
[0055] Wherein, the median may be the median of the Y-axis values of the sample points. Based on the characteristics that the characteristic data of the sensor is high first and then low, and the stable interval is the low numerical interval, this step can exclude the points in the undesired interval.
[0056] (2) Segment the extracted sample points.
[0057] Among them, the sample points can be segmented according to the X-axis data, because the change of the Y-axis data in the linear space is too small to be distinguished. The extracted sample points may be segmented...
PUM
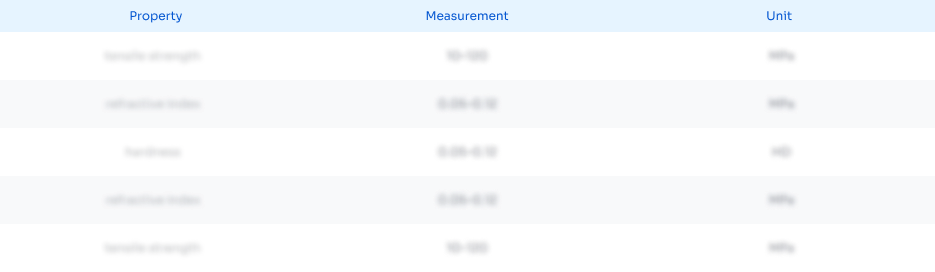
Abstract
Description
Claims
Application Information

- Generate Ideas
- Intellectual Property
- Life Sciences
- Materials
- Tech Scout
- Unparalleled Data Quality
- Higher Quality Content
- 60% Fewer Hallucinations
Browse by: Latest US Patents, China's latest patents, Technical Efficacy Thesaurus, Application Domain, Technology Topic, Popular Technical Reports.
© 2025 PatSnap. All rights reserved.Legal|Privacy policy|Modern Slavery Act Transparency Statement|Sitemap|About US| Contact US: help@patsnap.com