A transfer method for large area monolayer and few-layer molybdenum disulfide film
A technology of molybdenum disulfide and transfer method, which is applied in the direction of electrical components, semiconductor/solid-state device manufacturing, circuits, etc., and can solve the problems of inability to complete the transfer of molybdenum disulfide film, the quality of molybdenum disulfide film cannot be guaranteed, and it is difficult to clean and remove. , to achieve the effect of reducing film breakage, low cost and high repetition rate
- Summary
- Abstract
- Description
- Claims
- Application Information
AI Technical Summary
Problems solved by technology
Method used
Image
Examples
Embodiment 1
[0056] Molybdenum disulfide film (area 1mm 2 , the number of layers is 1-5 layers, and the thickness of each layer is 0.60-0.65nm) growth substrate (SiO 2 / Si substrate) is fixed on the glue leveler, drips a drop of polymethyl methacrylate phenethyl ether solution (polymethyl methacrylate concentration is 0.1g / mL) on the surface of described molybdenum disulfide film, with 2500rpm Speed spin coating 40s, repeat spin coating operation, totally spin coating 6 times, then solidify 20min under the condition of 80 ℃, form polymer film on the surface of described molybdenum disulfide film (thickness of described polymer film is 180nm );
[0057] BOPP biaxially oriented polypropylene scotch tape (glue composition is butyl ester, glue layer thickness is 25 μ m) is pasted on the surface of polymer film, do not leave air bubble, with scissors the tape of redundant part around described polymer film is cut off, Ensure that the size of the polymer film is consistent with that of the t...
Embodiment 2
[0062] Molybdenum disulfide film (with an area of 20mm 2 , the number of layers is 1 to 15 layers, and the thickness of each layer is 0.60 to 0.65nm) The growth substrate (sapphire substrate) is fixed on the glue homogenizer, and a drop of polydimethyl The phenetole ether solution of siloxane (the concentration of polydimethylsiloxane is 0.04g / mL), spin-coated at 1500rpm for 20s, repeated the spin-coating operation for a total of 3 times, and then at 150°C Carry out curing 5min, form polymer film (the thickness of described polymer film is 100nm) on the surface of described molybdenum disulfide film;
[0063] BOPP biaxially stretched polypropylene scotch tape (glue composition is butyl ester, glue layer thickness is 28 μ m) is pasted on the surface of polymer film, do not leave air bubble, with scissors the tape of redundant part around described polymer film is cut off, Ensure that the size of the polymer film is consistent with that of the tape; place the obtained sample ...
PUM
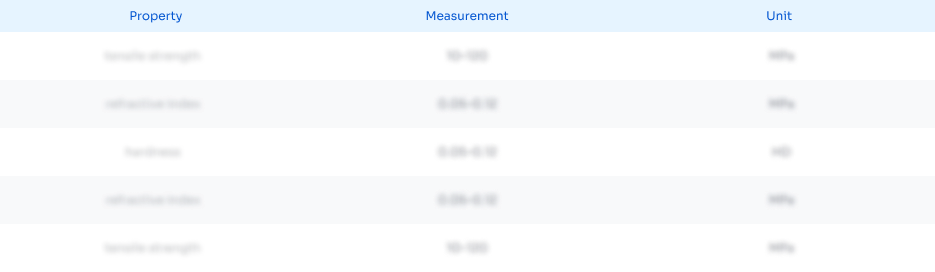
Abstract
Description
Claims
Application Information

- R&D
- Intellectual Property
- Life Sciences
- Materials
- Tech Scout
- Unparalleled Data Quality
- Higher Quality Content
- 60% Fewer Hallucinations
Browse by: Latest US Patents, China's latest patents, Technical Efficacy Thesaurus, Application Domain, Technology Topic, Popular Technical Reports.
© 2025 PatSnap. All rights reserved.Legal|Privacy policy|Modern Slavery Act Transparency Statement|Sitemap|About US| Contact US: help@patsnap.com