Composite turbomachine component and related methods of manufacture and repair
A technology for turbines and turbine blades, used in the manufacture of tools, engine components, mechanical equipment, etc., to solve problems such as cracking or other material fatigue
- Summary
- Abstract
- Description
- Claims
- Application Information
AI Technical Summary
Problems solved by technology
Method used
Image
Examples
Embodiment Construction
[0038] The subject matter disclosed herein relates to manufacture and / or repair. More specifically, the subject matter disclosed herein relates to composite components using materials having different coefficients of thermal expansion, and methods of forming those components.
[0039]Aspects of the present disclosure include composite turbine components, and methods of forming such components, as compared to conventional approaches. In various embodiments, a composite turbine component has a body and an insert filling a slot in the body, wherein the location of the slot is determined based on an expected or actual amount of material fatigue in the portion of the body. The insert may be welded to the body at the slot, but in some cases the insert may also be brazed to the body at the slot. In various embodiments, the body of the turbine component is formed from steel or an alloy, such as at least one nickel-chromium superalloy, at least one cobalt-based superalloy, or at least...
PUM
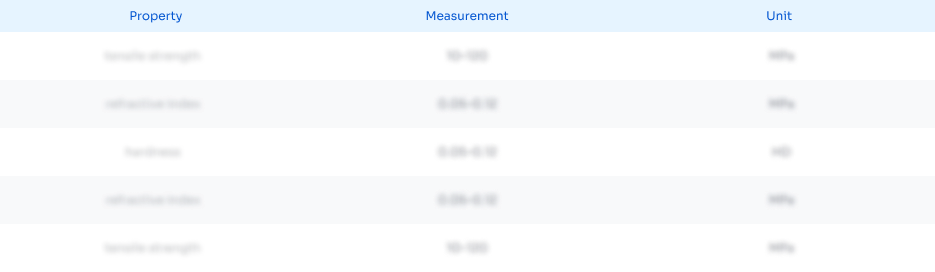
Abstract
Description
Claims
Application Information

- R&D Engineer
- R&D Manager
- IP Professional
- Industry Leading Data Capabilities
- Powerful AI technology
- Patent DNA Extraction
Browse by: Latest US Patents, China's latest patents, Technical Efficacy Thesaurus, Application Domain, Technology Topic, Popular Technical Reports.
© 2024 PatSnap. All rights reserved.Legal|Privacy policy|Modern Slavery Act Transparency Statement|Sitemap|About US| Contact US: help@patsnap.com