Preparation method of laser cladding coating
A laser cladding and coating technology, which is applied in the coating, metal material coating process, etc., can solve problems affecting the quality of laser cladding, and achieve the effect of ensuring the quality and uniform thickness of the cladding layer, and improving the strength and hardness
- Summary
- Abstract
- Description
- Claims
- Application Information
AI Technical Summary
Problems solved by technology
Method used
Image
Examples
Embodiment 1
[0044]Add the preset powder aluminum powder, titanium powder and carbon powder to ethanol according to the mass ratio of 6.4:1.8:1.8 and mix them, and put them into a ball mill for low-speed ball milling for 2 hours, and the ball milling speed is controlled at 480r / min to obtain a mixture of preset powders liquid;
[0045] Naturally air-dry the mixture of the above preset powders, and add Na 2 SiO 3 9H 2 O is mixed into a paste, among which, Na 2 SiO 3 9H 2 The mass ratio of O to the preset powder is 1:10;
[0046] Apply the pasty preset powder evenly on the pretreated ZL101 (ZAlSi 7 Mg alloy) and dried at 60°C for 11h, wherein the average thickness of the pasty preset powder coated on the surface of ZL101 is 1mm;
[0047] Place the above-mentioned ZL101 coated with preset powder on the processing platform of CNC milling machine, adjust the feed rate of CNC milling machine to 200mm / min, and the spindle speed to 1500r / min, and process the preset powder surface on the sur...
Embodiment 2
[0050] Add the preset powder aluminum powder, titanium powder and carbon powder to ethanol according to the mass ratio of 7.2:1.4:1.4 and mix them, and put them into a ball mill for low-speed ball milling for 1.6h, and the ball milling speed is controlled at 520r / min to obtain the preset powder. mixed solution;
[0051] Naturally air-dry the mixture of the above preset powders, and add Na 2 SiO 3 9H 2 O is mixed into a paste, among which, Na 2 SiO 3 9H 2 The mass ratio of O to the preset powder is 1:15;
[0052] Apply the paste-like preset powder evenly on the pretreated AZ91 (magnesium alloy), and dry it at 80°C for 7 hours, wherein the average thickness of the paste-like preset powder coated on the surface of AZ91 is 1.2mm;
[0053] Place the above-mentioned AZ91 coated with preset powder on the processing platform of CNC milling machine, adjust the feed rate of CNC milling machine to 260mm / min, and the spindle speed to 1400r / min, and process the preset powder surface ...
Embodiment 3
[0056] Add the preset powder aluminum powder, titanium powder and carbon powder to the deionized water according to the mass ratio of 7.8:1.1:1.1 and mix them, and put them into a ball mill for low-speed ball milling for 2.5 hours, and the ball milling speed is controlled at 520r / min to obtain the preset powder the mixture;
[0057] Dry the mixture of the above preset powders at a temperature of 100°C, and add Na 2 SiO 3 9H 2 O is mixed into a paste, among which, Na 2 SiO 3 9H 2 The mass ratio of O to the preset powder is 1:20;
[0058] Apply the pasty preset powder evenly on the pretreated ZL104 (ZAlSi 9 Mg) and dried at 70°C for 8h, wherein the average thickness of the pasty preset powder coated on the surface of AZ91 is 1.46mm;
[0059] Place the above-mentioned ZL104 coated with preset powder on the processing platform of CNC milling machine, adjust the feed rate of CNC milling machine to 220mm / min, and the spindle speed to 1600r / min, and process the preset powder s...
PUM
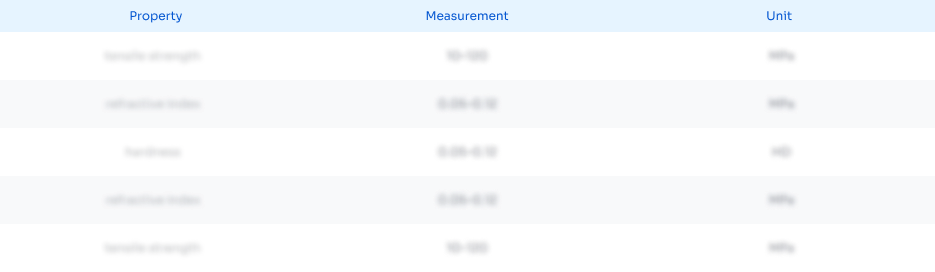
Abstract
Description
Claims
Application Information

- Generate Ideas
- Intellectual Property
- Life Sciences
- Materials
- Tech Scout
- Unparalleled Data Quality
- Higher Quality Content
- 60% Fewer Hallucinations
Browse by: Latest US Patents, China's latest patents, Technical Efficacy Thesaurus, Application Domain, Technology Topic, Popular Technical Reports.
© 2025 PatSnap. All rights reserved.Legal|Privacy policy|Modern Slavery Act Transparency Statement|Sitemap|About US| Contact US: help@patsnap.com