Manufacturing method of lithium slag lightweight ceramic panel
A technology of lightweight ceramics and production methods, which is applied in the direction of ceramic products, ceramic material production, clay products, etc., can solve the problems of inability to obtain qualified lightweight ceramic plate products, difficulty in forming a skeleton structure, and low melting temperature of green bodies, etc., to achieve The effect of saving energy consumption, reducing foaming temperature and reducing production cost
- Summary
- Abstract
- Description
- Claims
- Application Information
AI Technical Summary
Problems solved by technology
Method used
Examples
Embodiment 1
[0017] A manufacturing method of a lithium slag light-weight ceramic plate is made of the following raw materials: 30wt% lithium slag, 30wt% feldspar, 30wt% quartz powder, 7wt% alumina powder, and 3wt% foaming agent;
[0018] Its preparation method comprises the following steps:
[0019] 1) Take the raw materials for dry pulverization, and mix them in proportion to obtain the mixture; the fineness of alumina powder and quartz powder is required by the present invention to be less than 325 mesh, and sufficient fineness can promote the lithium, iron, and manganese elements in lithium tailings. Form a uniform mixture with external alumina and quartz powder;
[0020] 2) After adding water to the secondary mixture, stirring, granulating, drying, and sieving to obtain granular material;
[0021] 3) Put the granules into a sagger, lay them flat and then fire them, and obtain a light ceramic plate after cooling.
[0022] The foaming agent is silicon carbide.
[0023] The final firi...
Embodiment 2
[0026] A manufacturing method of lithium slag light-weight ceramic plates is made of the following raw materials: 65wt% lithium slag, 10wt% feldspar, 20wt% quartz powder, 4.8wt% alumina powder, and 0.2wt% foaming agent;
[0027] Its preparation method comprises the following steps:
[0028] 1) Take the raw materials and carry out dry powder milling, and mix them in proportion to obtain the mixture;
[0029] 2) adding water to the mixed material, stirring, granulating, drying, and sieving to obtain the granular material;
[0030] 3) Put the granules into a sagger, lay them flat and then fire them, and obtain a light ceramic plate after cooling. The foaming agent is silicon carbide.
[0031] The final firing temperature in step 3) is 1030-1130 degrees.
[0032] The content of ferric oxide in the lithium slag is not higher than 30wt%, and the content of manganese monoxide is not higher than 10%.
Embodiment 3
[0034] A manufacturing method of lithium slag light-weight ceramic plate is made from the following raw materials: 50wt% lithium slag, 20wt% feldspar, 18wt% quartz powder, 10wt% alumina powder, and 2wt% foaming agent;
[0035] Its preparation method comprises the following steps:
[0036] 1) Take the raw materials and carry out dry powder milling, and mix them in proportion to obtain the mixture;
[0037] 2) adding water to the mixed material, stirring, granulating, drying, and sieving to obtain the granular material;
[0038] 3) Put the granules into a sagger, lay them flat and then fire them, and obtain a light ceramic plate after cooling.
[0039] Further, the foaming agent is silicon carbide.
[0040] Further, the final firing temperature in step 3) is 1030-1130 degrees.
[0041] Further, the content of ferric oxide in the lithium slag is not higher than 30wt%, and the content of manganese monoxide is not higher than 10%.
[0042] For the lightweight ceramic plates pre...
PUM
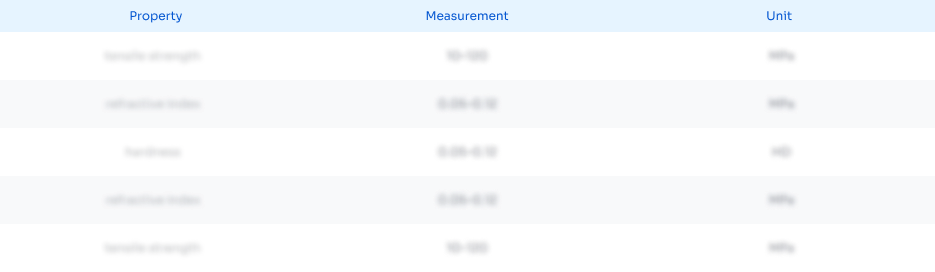
Abstract
Description
Claims
Application Information

- Generate Ideas
- Intellectual Property
- Life Sciences
- Materials
- Tech Scout
- Unparalleled Data Quality
- Higher Quality Content
- 60% Fewer Hallucinations
Browse by: Latest US Patents, China's latest patents, Technical Efficacy Thesaurus, Application Domain, Technology Topic, Popular Technical Reports.
© 2025 PatSnap. All rights reserved.Legal|Privacy policy|Modern Slavery Act Transparency Statement|Sitemap|About US| Contact US: help@patsnap.com